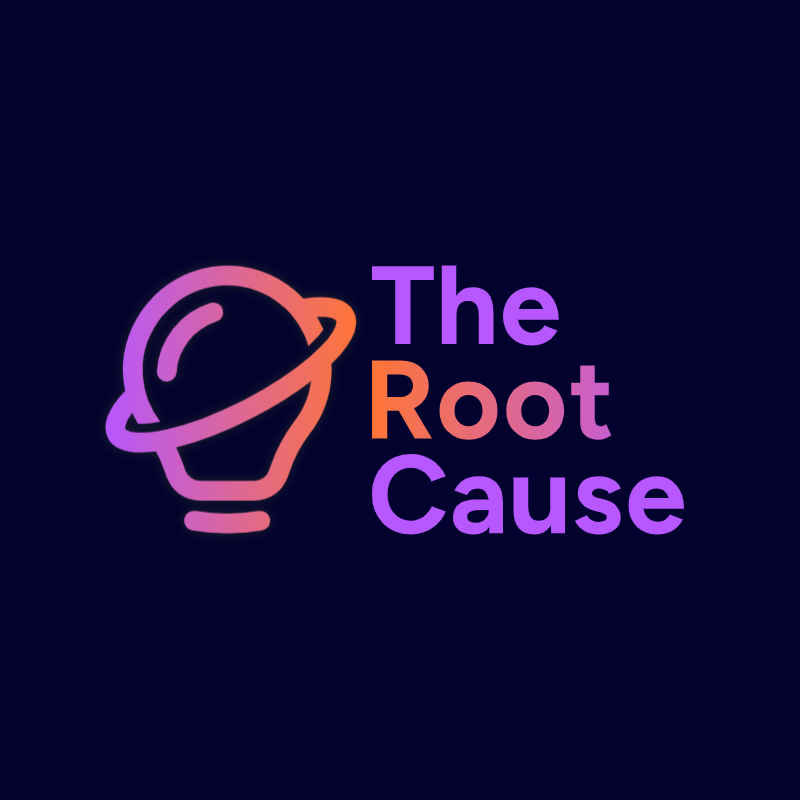
Ep 14. The Critical Role of Human-Centric UX/UI Design on the Factory Floor
The Root Cause Podcast Ep. 14 - The Critical Role of Human-Centric UX/UI Design on the Factory Floor
In this episode of The Root Cause, we dive into a fascinating study on UX/UI design in manufacturing and how modernizing factory interfaces can dramatically boost efficiency, safety, and workforce satisfaction. Make sure to stay tuned until the end for a special announcement on our TME® platform!
[A: 00:08.0]
Welcome back, everybody. Today we're going to be doing a deep dive into something that's super important in manufacturing, but I feel like doesn't get talked about enough, and that is user interface design. Specifically on the factory floor and how it can really impact operations.
[B: 00:23.4]
Yeah, you know, it's funny. UI design is one of those things that sort of gets pushed to the back burner when we talk about, you know, advancements in technology.
[A: 00:31.1]
Right.
[B: 00:31.5]
But I think it's becoming more and more clear that especially in today's, like, fast paced production environments, you need to have an interface that people can use quickly and efficiently.
[A: 00:43.6]
Exactly. But it's way more important than people realize. We're not just talking about making screens look pretty. This is about making work better.
[B: 00:52.5]
Absolutely. I mean, the human element is still key. Right. In any factory, no matter how automated it gets.
[A: 00:57.9]
Totally. And how people interact with the systems, the machines, the processes it can make or break, efficiency, safety, everything.
[B: 01:05.7]
No doubt. And to really get why this is so important, we need to take a hard look at what's happening on a lot of factory floors right now.
[A: 01:12.3]
Okay, paint me a picture. What's the current state of things?
[B: 01:15.7]
Well, some research out of Tampere University of Technology in Finland. They interviewed 25 different manufacturing companies, and what they found is, well, pretty surprising, actually.
[A: 01:27.0]
Really? What did they find?
[B: 01:28.9]
A lot of companies, they're still using, get this, paper based systems.
[A: 01:34.0]
Paper!
[B: 01:34.7]
Seriously.
[A: 01:35.5]
Seriously! We're talking work orders, scheduling, quality checks, even just tracking time on tasks, all on paper.
[B: 01:43.5]
Wow. I could already see where this is going. Not exactly the picture of efficiency.
[A: 01:46.7]
Not even close
[B: 01:47.8]
And the potential for mistakes has gotta be huge with paper. Huge. And that's one of the biggest reasons companies are going digital. Of course. But. And this is a big but. A lot of those digital systems, they're not much better.
[A: 02:01.3]
Oh, so they're trading one problem for another?
[B: 02:04.1]
Kinda, yeah. A lot of the interfaces are clunky, hard to use. They weren't designed with the people who actually use them in mind.
[A: 02:11.7]
So it's like trying to force a square peg into a round hole.
[B: 02:14.8]
Perfect analogy. You're trying to make people work in a way that just doesn't make sense. And that leads to frustration, mistakes, people resisting the technology altogether.
[A: 02:23.3]
Oof. That's recipe for disaster. And that's where good UX/UI design comes in, I guess.
[B: 02:28.2]
Bingo. It's all about understanding the needs, the workflows, even the way people think. And then designing an interface that feels natural, intuitive, like it was made for them.
[A: 02:38.7]
It's really human centered design. Even in a high tech factory.
[B: 02:41.8]
Exactly. And when you get it right, the benefits are huge. So streamlined tasks, fewer errors, even happier workers.
[A: 02:49.1]
Happier workers. Now that's something I want to hear more about.
[B: 02:52.0]
This research, it showed that good UI can sometimes cut the clicks needed for a task by 50%.
[A: 02:58.0]
50%? That's gotta save a ton of time.
[B: 03:00.5]
Oh yeah, and in manufacturing, time is money. Right, but it goes beyond that too. When people are wrestling with a clunky system all day, they get frustrated.
[A: 03:10.3]
Totally. Makes sense. I mean, nobody wants to be stuck with a tool that makes their job harder.
[B: 03:14.9]
Exactly. It leads to mistakes, less productivity, even people quitting. But when they have tools that are easy to use, tools that help them do their jobs well, they feel good.
[A: 03:26.1]
Okay, so it's good for morale, good for business.
[B: 03:28.5]
Win, win. And think about attracting talent, especially the younger generation. They've grown up with sleek tech. They expect it everywhere. True.
[A: 03:36.2]
They're not gonna put up with clunky systems.
[B: 03:37.8]
Yeah.
[A: 03:38.2]
So good design makes manufacturing jobs more appealing, more competitive.
[B: 03:42.1]
Absolutey. So we've talked about the bad, but what about the good? What does good UX/UI design actually look like on the factory floor?
[A: 03:49.8]
Yeah, I'm all ears . Spill the secrets of good design.
[B: 03:53.0]
Well, one of the big things is what we call speaking the user's language.
[A: 03:56.7]
Okay, intrigue me. What does that even mean?
[B: 03:59.1]
Simple. Use terms and symbols that the workers already know. Ditch the jargon, ditch those abstract icons. Make it clear, concise, easy to understand.
[A: 04:08.0]
Got it. Keep it simple, stupid. Right.
[B: 04:10.6]
Basically, you want to reduce that mental load, make it easy to process information quickly, especially on a busy factory floor.
[A: 04:17.7]
Makes perfect sense. So speak their language. What else?
[B: 04:21.3]
Clear feedback. Gotta let users know what's happening every step of the way.
[A: 04:26.5]
Like, is the task running? Did it work? Anything like that?
[B: 04:29.0]
Exactly. Progress bars, confirmation messages, clear error alerts. Those little things make a huge difference.
[A: 04:35.5]
I bet. Makes people feel confident, like they're in control.
[B: 04:38.5]
And on the factory floor, where safety is so crucial, you don't want people guessing, right?
[A: 04:42.7]
Oh, absolutely. But how do you actually implement all this stuff? It seems like taking those design principles and making them work in the real world on a factory floor, that's got to be tough.
[B: 04:52.7]
Oh, it definitely takes planning and effort, but there are companies out there doing it really well.
[A: 04:58.0]
Oh, I bet. So what's their secret?
[B: 05:00.1]
One big thing is getting the workers involved, like from the very beginning.
[A: 05:03.9]
Ah. So don't just assume you know what they need. Ask them.
[B: 05:07.4]
Exactly. Observe them, understand their challenges, get their feedback on designs.
[A: 05:12.3]
Sounds like a lot of collaboration, a lot of empathy.
[B: 05:14.6]
Absolutely. But it goes beyond just talking. You got to gather data on how they're using the system track eye movements, click patterns, how long it takes them to do stuff.
[A: 05:23.8]
Okay, so get the data to back up your design choices. No more guesswork.
[B: 05:27.8]
Right. And then you use that data to make things better. Tweaking the interface, making it smoother, more efficient.
[A: 05:33.0]
A constant improvement cycle. Kind of like in lean manufacturing.
[B: 05:36.6]
Exactly. Good UX design and lean manufacturing, they actually have a lot in common. But both focused on cutting waste, boosting efficiency, streamlining everything.
[A: 05:45.4]
Both looking at the whole picture and how to make the human element work best within that picture.
[B: 05:50.5]
You got it. Which brings us to another critical piece of the puzzle. Real time data.
[A: 05:55.9]
Ah, real time data. The lifeblood of any modern operation, especially in manufacturing. Right?
[B: 06:01.6]
Huge. Yeah. In the past, managers had to rely on reports that were like ancient history, days or weeks old.
[A: 06:08.2]
Ouch. That's going to make it tough to make good decisions.
[B: 06:11.0]
Tell me about it. But with real time data, you've got your finger on the pulse. You see production, machine, performance, inventory, everything updated constantly.
[A: 06:20.5]
That's going to be so valuable. No more flying blind. You actually have the information you need when you need it.
[B: 06:26.4]
Exactly. Makes for faster, smarter decisions. Like imagine a machine breaks down. You see the impact instantly and can react right away.
[A: 06:33.5]
Proactive, not reactive. You're heading off problems before they become disasters.
[B: 06:37.5]
You got it. And that agility, that's a huge advantage in today's world.
[A: 06:41.0]
Big time. I'm also thinking about quality control, waste reduction. If you can see trends, see problems in real time, you can stop them before they become big issues.
[B: 06:51.8]
Absolutely. Real time data. It empowers everyone from operators to managers to make ton choices to work smarter.
[A: 06:59.4]
Like having a crystal ball, but instead of magic, it's powered by data.
[B: 07:03.2]
Haha. I like that. And speaking of real world examples, there's this company that just revamped their entire Manufacturing Execution System and it's like the perfect example of what we're talking about.
[A: 07:14.1]
Oh, really? Tell me more. What did they do?
[B: 07:16.3]
Well, they took the system. It had been around for a while and frankly it was a bit clunky. Not very user friendly.
[A: 07:22.0]
Yeah, we've all been there. That software that makes you want to pull your hair out.
[B: 07:25.0]
Exactly. But they took this clunker and gave it a complete makeover. Focused on the user experience, made it actually enjoyable to use.
[A: 07:33.7]
Okay, I'm hooked. Tell me everything.
[B: 07:35.5]
All right, so first they modernized the whole look and feel, made the navigation intuitive. But the really cool part is how they simplified the workflows.
[A: 07:45.8]
Okay, tell me about those workflows.
[B: 07:47.7]
So one example, configuring a work in progress workflow, they cut the number of clicks in half.
[A: 07:54.0]
Half? That's huge. Those little clicks, they add up over time, you know.
[B: 07:58.6]
Oh yeah, and it's not just about speed. They made the whole system way more responsive. Data updates in real time, no more lag.
[A: 08:06.5]
So you can really see what's happening right as it happens. That's gotta be a game changer.
[B: 08:09.8]
Totally. And get this, they made it mobile friendly. Tablets, smartphones, you name it.
[A: 08:14.3]
Wow. So no more being chained to a desktop. You can access information from anywhere on the factory floor.
[B: 08:19.9]
You got it. And they added things like zoom functionality so you can enlarge text without it getting blurry.
[A: 08:26.6]
That's fantastic. Especially for accessibility. Not everyone has perfect vision and being able to adjust the display is so important.
[B: 08:34.4]
Totally agree. It shows they were really thinking about the user. Every user.
[A: 08:38.8]
This whole update, it's a perfect example of what we've been talking about. Putting the user first, making work better, not just prettier.
[B: 08:45.9]
Couldn't have said it better myself. And you know, it's not just about the individual good UX/UI design. It impacts the whole organization.
[A: 08:52.7]
It's the chain reaction.
[B: 08:53.7]
Right?
[A: 08:54.2]
People are happier, they're more productive, the quality goes up, the whole business wins.
[B: 08:58.0]
Exactly. It's a win win for everyone.
[A: 09:00.1]
This has been a fascinating deep dive. It's amazing how something like UX/UI design, which you don't always think about in a factory setting, is, can be so impactful.
[B: 09:08.6]
It's definitely an often overlooked area, but it's crucial for creating a modern, efficient and human centered workplace.
[A: 09:15.9]
Well said. And as technology keeps evolving and manufacturing gets more complex, the role of good design is only going to become more important.
[B: 09:24.7]
No doubt about it. It's an investment that pays off in so many ways.
[A: 09:28.1]
Absolutely. Now, before we wrap up, a big thank you to our sponsor for making this episode possible.
[B: 09:33.4]
Yes, thank you to MASS Group. They're a leading provider of, you guessed it Manufacturing Execution and Asset Management software.
[A: 09:42.3]
And speaking of MASS group, they just released a major update. You might have heard of it.
[B: 09:46.8]
It's called TME® 8.0.
[A: 09:49.4]
The one we've been hinting at this whole time?
[B: 09:51.5]
The very same. It's a total revamp, focused on the user experience, streamlining all the features.
[A: 09:57.5]
If you're in the market for a system that's both powerful and easy to use TME® 8.0 is definitely worth checking out
[B: 10:04.5]
For sure.
[A: 10:05.2]
And for our listeners, we want to hear from you What aspects of UI design are most important in your work?
[B: 10:10.6]
Yeah, share your thoughts in the comments.
[A: 10:12.1]
We love hearing your experiences. Until next time, keep diving deep.
[B: 10:16.1]
See you all next time.
Read the Full Study from Applied Sciences here.
Subscribe to The Root Cause Podcast on YouTube or follow MASS Group on LinkedIn for more insights into manufacturing, automation, and innovation. Stay tuned for more episodes that dive deep into The Root Cause!