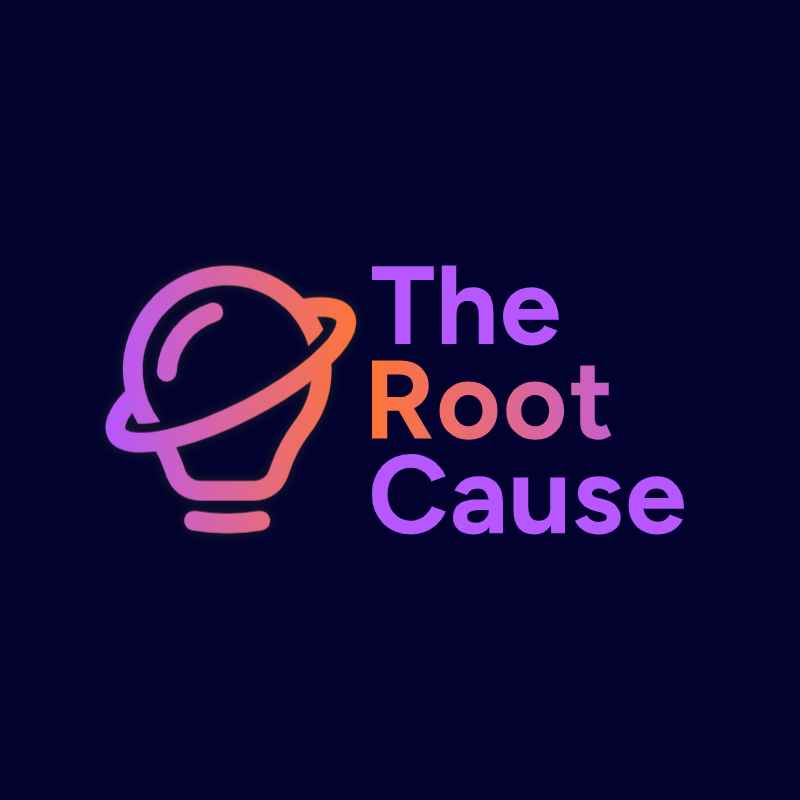
Turning Real-Time Data into Actionable Insights with Power BI
The Root Cause Podcast Episode 2 - Using PowerBI to gain Actionable Insights from Real-Time Data
Welcome back to The Root Cause, a podcast series where we explore key trends, challenges, and innovations at the heart of manufacturing. After the great response to Episode 1, we’re excited to dive into a topic that’s transforming modern manufacturing—how to turn real-time data into actionable insights. In this episode, we’ll take a closer look at the role of Power BI and how it integrates with Manufacturing Execution Systems (MES) to bring powerful data visualization and smarter decision-making to the factory floor.
What We Explore in Episode 2:
- Collecting data isn’t enough—contextualizing it is key
- Power BI + MES = powerful data visualization and insights
- The shift from reactive maintenance to predictive maintenance
- Automation isn’t replacing workers—it’s empowering them
- TME®'s Power BI integration for smarter operations
All right, everyone, let's talk manufacturing.
Specifically, how real time insights are
revolutionizing the way things are done.
What's fascinating here is the shift from
reacting to problems after they occur to
anticipating and preventing them altogether.
It's like having a crystal ball for your factory floor.
Exactly.
Okay, let's unpack this.
We're talking granular, real time data.
Wow.
Talk about having your finger on the pulse.
Absolutely.
That's incredible.
Precisely.
And the ability to make data driven decisions on the
fly is a game changer for manufacturers of all sizes.
Now, you know me, always looking for that aha moment.
So let's talk about why this matters.
Let's say I'm a plant manager.
How does catching a temperature blip
translate to real value for me?
It's not just about catching the blip.
It's about what you avoid because of it.
Unexpected downtime in manufacturing can cost thousands, even
tens of thousands of dollars per hour.
Okay
so real time insights
aren't just preventing a headache.
They're potentially saving you a small fortune.
Okay, now you're talking my language.
Yeah, but let's shift gears a bit.
We keep mentioning this data, but
let's not forget the human element.
How do we get everyone on the factory
floor on board with this data driven approach?
You're absolutely right.
The most sophisticated data in the world is
useless if it's not accessible and understandable to
the people who need to use it.
That's where a data first culture comes in.
So no more data silos.
Everyone's speaking the same language.
Precisely.
And to achieve that, we need systems that
can handle this constant influx of information.
Think of it like building a central nervous
system for the factory of the future.
That's where Manufacturing Execution Systems,
or MES, come into play. Right?
It's like the brains of the operation.
Exactly.
MES is the backbone of a connected factory.
It's the system that collects data from
all those machines and sensors, organizes it,
and makes it available for analysis.
So it's like the ultimate data collector.
But it's gotta be more than that, right?
A good MES doesn't just
collect data, it contextualizes it.
Let's say your MES flags the slowdown in line three.
It's not just telling you there's an issue.
It can show you historical data.
Maybe this always happens when a certain raw material
is low, prompting you to check inventory levels.
Okay, now, that's what I'm talking about.
Connecting the dots.
But let's not forget we're talking about
potentially massive amounts of data here.
How do we make sense of it all.
I can see this easily.
Turning into information overload territory.
That's the challenge, isn't it?
Turning data into insight
It's not enough to have the data.
You need to visualize it, analyze it,
and extract those golden nuggets of knowledge.
So it's like finding the signal in all the noise.
Exactly.
And that's where the right tools come in.
We need something to help us unlock
the full potential of all this data.
Enter Power BI right?
I have a feeling this is where
our MES story gets really interesting.
You got it.
So think of MES
As, like, the brains of the operation
They're gathering all that data from your sensors,
from your machines, your systems, organizing it, and
starting to make sense of it.
Okay
But then imagine trying to like
decipher thousands of lines of code.
Yeah
You need a way to translate
that data into something understandable, right?
So you need something that can speak human.
Exactly.
That's where Power BI steps in.
Power BI steps in. Right.
It's like the great translator in this whole scenario.
Exactly.
Okay.
It takes all that complex data from the MES
and turns it into something that anyone, you know,
even if you're not a data scientist, can understand.
Clear, visual, like dashboards, charts, reports.
So instead of getting lost in a sea of numbers.
Yeah.
A production manager could glance at his
screen and instantly see, you know.
Yeah.
If a particular line is hitting its targets.
Okay.
Or if there's a bottleneck slowing things down.
So it's about making that data actionable.
Exactly.
It's one thing to have it.
It's another thing to actually be able
to understand it and use it
By analyzing historical data from your MES,
Power BI can identify patterns that might
indicate an impending equipment failure.
It's about using data to anticipate
problems before they impact your operations.
So instead of waiting for a machine to
break down and then scrambling to fix it,
you're able to schedule maintenance proactively, minimizing downtime
and keeping things running smoothly.
It's like having a crystal ball for your factory.
It's like shifting from reactive
maintenance to predictive maintenance.
Instead of fixing problems as they arise,
you're anticipating and preventing them altogether.
That's incredible, but let's get specific.
We've talked about predictive maintenance, but what are
some other concrete benefits manufacturers can expect from
a strong MES and Power BI integration?
The possibilities are truly vast, but let's
focus on a few key areas.
First, workflow optimization.
By visualizing production data, you can
identify bottlenecks, streamline processes, and ensure
that resources are being used efficiently.
This can lead to significant
improvements in productivity and throughput.
So no more guessing games.
When it comes to efficiency, you have
the data to back up your decisions.
Precisely.
It's about replacing gut feelings
with data driven insights.
And this data driven approach extends
to every aspect of your operation,
from inventory management to quality control.
And let's not forget the holy
grail of any business, increased profitability.
How does all of this translate to the bottom line?
It's simple, really.
By reducing downtime, optimizing workflows, and making
better decisions across the board, you're ultimately
saving money and boosting your bottom line.
It's amazing to think that something as
seemingly complex as data analytics can actually
lead to such tangible and impactful results.
It's not just about the numbers, though.
It's about empowering people at every level
of the organization to make smarter decisions.
So it's not just about replacing human intuition, it's
about enhancing it with the power of data.
Precisely.
It's about giving your team the information they need
to do their jobs better, faster, and more efficiently.
All right, enough teasing.
Give me the details.
What does this dream team of MES
and Power BI
look like in action?
Yes, MASS Group has
Just announced a seamless integration of
Power BI directly into their platform.
Wow.
So no more juggling separate systems
or struggling to connect the dots. That's huge.
Exactly.
It's all about making powerful data analysis accessible
and intuitive for everyone on the manufacturing floor.
It's one thing to have all of
this data at your fingertips, but it's
another thing to actually use it effectively.
Exactly.
And that's what I find
so compelling about this integration.
It's not just about giving people access to data
It's about empowering them to understand it,
to use it to make informed decisions,
no matter their role in the company.
So it's less about being intimidated by data and more
about embracing it as a tool for continuous improvement.
Precisely.
It's about creating a culture where everyone
from the shop floor to the top
floor is speaking the same language.
The language of data.
This has been a fascinating deep dive.
We've explored the incredible power of MES and
Power BI, and how MASS Group is making
these tools more accessible than ever before.
It really feels like we're on the
cusp of a new era in manufacturing.
An era driven by data insights
and a relentless pursuit of efficiency.
Couldn't agree more.
It's an exciting time to be in this industry,
and I'm eager to see how manufacturers leverage these
tools to push the boundaries of what's possible.
Well said.
As we wrap up, I can't help but
wonder what the future holds for manufacturing.
Where do we go from here?
That's the exciting part.
We're standing on the precipice of a new era
in manufacturing driven by data connectivity and automation.
This is just the beginning.
As technology continues to evolve, the potential for
real time insights will only continue to grow.
And on that note, we'll wrap up this deep dive.
Thanks for joining us on this fascinating journey into
the world of real time insights in manufacturing.
Episode 2: Power BI + MES = Game-Changing Insights
At MASS Group, we’ve integrated Power BI into our Traceability Made Easy (TME®) platform to deliver seamless data insights to manufacturers. In this episode, we explore how combining Power BI’s intuitive data visualization with MES technology helps companies make sense of their data and take immediate, informed action.
By connecting Power BI to an MES like TME®, manufacturers can create real-time dashboards that allow them to:
- Visualize production trends
- Monitor equipment performance
- Track work-in-progress (WIP)
- Identify inefficiencies
- Streamline operations for better results
This level of integration enables manufacturers to shift from just collecting data to truly understanding and using it for continuous improvement.
Why Data Alone Isn’t Enough
Manufacturers collect massive amounts of data daily, but data alone doesn’t improve operations. What matters is how that data is contextualized and used to drive meaningful insights. Raw numbers without a story or context can leave manufacturers reactive to issues instead of proactive. That’s why real-time analytics and data visualization tools like Power BI are game-changers—they help manufacturers see trends, make predictions, and take action before problems arise.
Moving from Reactive to Predictive Maintenance
One key discussion in Episode 2 revolves around maintenance strategies. Historically, many manufacturers have relied on reactive maintenance, meaning they address equipment issues only after they happen. This approach can lead to unplanned downtime and higher repair costs. With real-time data analytics, manufacturers can transition to predictive maintenance, where equipment health is monitored in real-time, and potential failures are detected before they happen. This shift allows companies to proactively address issues, reduce downtime, and improve overall equipment efficiency.
The Role of Automation: Empowering, Not Replacing
Automation is another hot topic in today’s manufacturing landscape. Many fear that automation will replace jobs, but the truth is, automation empowers workers to be more productive and focused on high-value tasks. In Episode 2, we explore how the integration of real-time data and automation is freeing workers from repetitive tasks, allowing them to focus on more strategic work. This creates a more empowered, skilled workforce that can leverage automation as a tool for innovation rather than a replacement.
TME® and Power BI: A Smarter Approach to Manufacturing Operations
At MASS Group, we’re dedicated to helping manufacturers get the most out of their data. By combining the powerful analytics capabilities of Power BI with the real-time operational data from TME®, we’re enabling smarter, faster decision-making. Manufacturers can create dashboards customized to their needs, giving each team member—from operators to managers—the information they need to drive results.
What’s Next?
In Episode 2 of The Root Cause, we’ve scratched the surface of how real-time data and advanced analytics are transforming manufacturing operations. But there’s so much more to come! In future episodes, we’ll dive deeper into the role of automation, advanced maintenance strategies, and the future of manufacturing innovation.
We invite you to follow MASS Group on LinkedIn or subscribe to our YouTube channel to stay updated on new episodes. And as always, feel free to join the conversation! Comment, share your thoughts, and let’s work together to uncover the root causes of the industry’s biggest challenges.