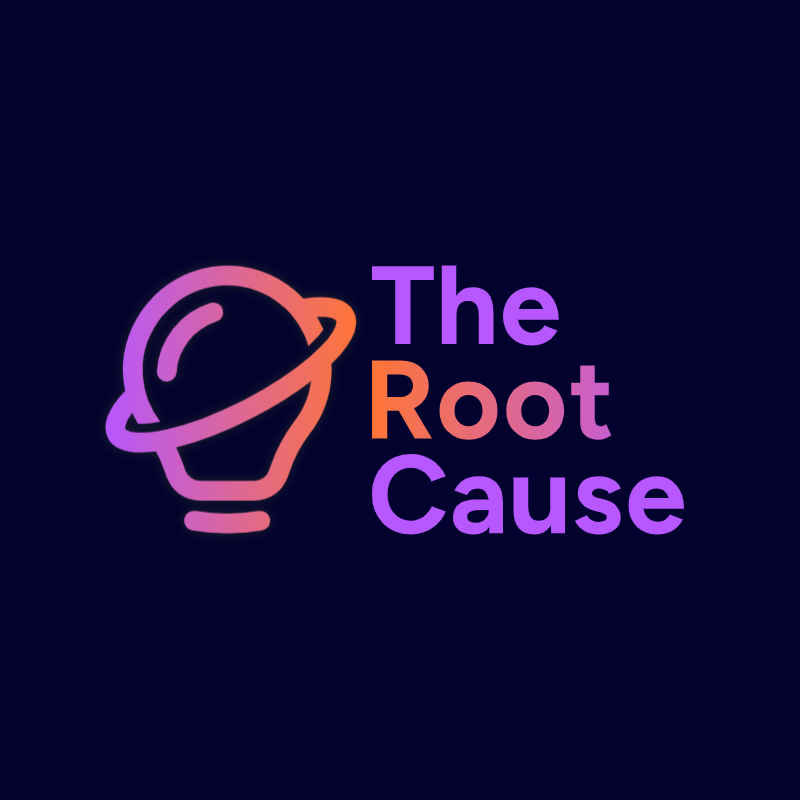
Ep. 5 The Evolution of Root Cause Analysis: The Five Why's, The Eight Disciplines (8D), and Beyond
The Root Cause Podcast Episode 5 – Breaking Down the Evolution of Root Cause Analysis
Welcome to the latest episode of The Root Cause, where we’re taking you on a journey through the evolution of root cause analysis in manufacturing. From Henry Ford’s early assembly lines to Toyota’s iconic Five Why's and Ford Motor Company’s Eight Disciplines (8D) process, discover how these foundational methods have paved the way for the advanced problem-solving tools used in today’s high-tech factories.
Root cause analysis has evolved from basic troubleshooting techniques to advanced methodologies that define modern manufacturing excellence. This episode is essential for anyone in manufacturing, quality management, or operations who wants to understand the history, present, and future of this critical discipline.
What We Explore in Episode 5:
- Ford’s foundational problem-solving methods in early manufacturing
- Toyota's creation of the Five Why's for drilling down to root causes
- The Eight Disciplines (8D) and how it transformed collaborative problem-solving
- Modern MES systems and how they apply real-time insights for faster resolution
- The future of root cause analysis with AI and automation
into root cause analysis
Yeah
specifically in manufacturing.
Absolutely. It's fascinating.
Yeah.
You know, going beyond just fixing a problem, figuring
out why it happened in the first place.
Right.
Getting to the bottom of it.
Yeah, the evolution of problem solving.
It really highlights how crucial this has been
in manufacturing for a very long time.
Oh, I bet.
You know, I mean, every minute that
a factory's down, that's money lost.
Right.
Quality issues can really hurt
a company's reputation for sure.
And any inefficiencies are just eating away at profits.
So this isn't just like a nice to have, huh?
Absolutely not.
This is about survival in a competitive market.
Yeah, yeah.
Okay, so let's rewind the clock
back to the early 1900's.
picture Henry Ford.
Not just the assembly line genius,
but a problem solving pioneer.
Now that's a side of Ford I
bet most people don't know
right?
Most folks associate him with the
Model T in mass production.
But here's where things get interesting.
That very assembly line he created actually forced
him to become a problem solving ninja.
Think about it
One tiny snag, one part out of place, and boom.
The whole operation could grind to a halt.
Like a giant domino effect.
One wrong move, and the whole line falls apart.
So Ford, being the innovator, he was simplified
and standardized processes to minimize those errors.
And get this.
He did all this way before
quality control was even a thing.
He was ahead of his time, that's for sure.
These ideas really laid the groundwork for
what we consider standard practice today.
Absolutely.
So while Ford was busy standardizing
over in America, across the Pacific,
another manufacturing powerhouse was emerging: Toyota.
And these guys took problem solving to
a whole new level with their continuous
improvement philosophy, also known as kaizen.
Ah, kaizen.
It's like a mantra in the manufacturing world.
Always striving for better, never settling.
Right.
And from this relentless pursuit of improvement
came a tool that sounds deceptively simple.
The Five Why's.
The Five Why's are incredibly powerful.
Imagine peeling back the layers of an
onion, each why revealing another layer of
the problem until you reach the core.
It's about forcing yourself to look beyond
the obvious and uncover the real culprit.
Okay, so for those listening who haven't actually tried
the Five Why's, give us a real world example.
I mean, can we apply this outside of a factory setting?
Absolutely.
Let's say your Internet suddenly goes out.
Super frustrating, right?
So you ask, why is the Internet down?
Maybe the router's acting up.
But you don't stop there.
You dig deeper and ask, why is the router not working?
Could be a power outage.
Why is there a power outage?
You check your phone and boom.
A neighborhood wide outage is reported. See?
Just three whys and you've gone from blaming
your router to understanding the bigger picture.
That's a perfect example. And you know what?
I'm starting to realize how useful the Five
Why's could be for, well, almost any problem.
It's like a mental detective tool.
Exactly.
And it's a fantastic starting point for more complex
problem solving methods like the 8D process, which Ford
Motor Company developed later in the 1980s.
Now from what I've read, 8D is like
the big brother of the Five Why's.
Way more structured, more collaborative.
You could say that manufacturing was
becoming increasingly complex and those simple
why questions just weren't enough anymore.
So Ford Motor Company came up with the 8D
process, which stands for eight disciplines of problem solving.
Basically, a super systematic way to tackle those
tougher problems with a whole team on board.
Okay, so it's all about bringing order
to the chaos of a problem.
Love it.
But a roadmap with eight steps?
I'm already feeling a bit overwhelmed.
Uh huh, I hear you.
It does sound a bit daunting at first, but
trust me, there's a logic to the madness.
Each step builds on the one before it.
Okay, so walk us through those steps.
What's the first crucial move
in this 8D detective story?
The first step, and arguably the
most important, is assembling your team.
You need the right people with the right expertise.
Kind of like gathering your best detectives for a case.
Then you move on to clearly defining the problem.
This is where those observation skills come in.
Gathering all the facts, data and symptoms.
Just like a detective examining the crime scene.
Got.
So it's all about setting the stage
and getting everyone on the same page.
What happens next?
Do we jump into full on Sherlock mode?
Not quite yet.
The third discipline is about taking quick
action to contain the problem, prevent it
from spreading or causing more damage.
Think of it as putting up those
yellow caution tapes around the crime scene.
Makes sense.
Yeah.
So it's damage control before diving
into the why behind it all.
Exactly.
And that brings us to the heart of the 8D process.
Root cause analysis.
This is where you pull out all the stops.
Brainstorming, using tools like the five
whys, analyzing data, and really digging
deep to uncover the root cause.
It's like putting those detective skills to the
test, examining the clues and connecting the dots.
Absolutely.
And once you've identified the root cause, the next
step is figuring out how to fix it.
This involves developing a corrective action
plan, essentially coming up with a
strategy to neutralize the culprit.
So we've gone from defining the problem to understanding
the why, and now we're ready to take action.
What comes next?
Well, it's time to implement those corrective
actions, making sure they actually work and
the problem is truly solved.
This is like apprehending the culprit and making
sure they're off the streets for good.
But the case isn't closed just yet. Right?
What about preventing the problem from happening again?
You're one step ahead of me.
The seventh discipline is all about prevention.
This is where you put measures in place to make
sure the problem doesn't rear its ugly head again.
Think of it as installing a state of the
art security system to prevent future break ins.
Love the analogy.
So we've solved the mystery, caught the
bad guy, and put safeguards in place.
What's the final step?
The last but certainly not least, discipline
is all about recognizing your team's success.
After all, cracking a tough
case deserves a celebration, right?
Absolutely.
It's about acknowledging all that hard work
and fostering that sense of teamwork.
Exactly.
And celebrating success also reinforces that
continuous improvement mindset, encouraging everyone to
keep those problems solving skills sharp.
Okay, so we've got Ford standardization,
Toyota's Five Why's, and now Ford Motor
Company's super systematic 8D process.
It's fascinating to see how this idea of
root cause analysis has evolved over time.
But I have to ask, with
all the amazing technology available today
Are these older methods still relevant?
That's a great question, and
the answer might surprise you.
These so called old school methods
are more relevant than ever.
They've actually paved the way for
the incredibly sophisticated problem solving technology
used in factories today.
Things like real time data analysis,
automation, and those Manufacturing Execution Systems or
MES, that you hear so much about.
Okay, so it's like these
classic methods have gone digital.
Tell me more about how these
MES systems are changing the game.
Well, imagine having a detective with access to a real
time feed of everything happening at the crime scene.
That's essentially what an MES
system does for a factory.
They're constantly collecting and crunching data from
every corner of the production floor, giving
manufacturers an incredible level of visibility.
So it's like having a bird's
eye view of the entire operation 24/ 7.
Exactly.
And that level of visibility allows
manufacturers to spot problems much earlier,
sometimes even before they actually occur.
Wait, so they can predict the future?
That sounds a bit like science fiction.
Not quite predicting the future,
but getting pretty close.
These systems can analyze historical data and
real time trends to identify patterns that
might indicate a problem brewing.
It's like noticing that the same suspect
keeps hanging around the jewelry store.
A red flag that something might be up.
That's amazing.
So it's all about being proactive
and preventing problems rather than reacting
after they've already caused chaos.
Exactly.
And that's where the link to those
classic root cause analysis methods comes in.
Remember how we talked about the importance
of identifying the why behind a problem?
Well, MES systems can be a powerful tool for this too.
Okay, I'm intrigued how they do that.
By providing detailed data on every single step
of the production process, an MES system can
pinpoint exactly where a problem originated.
It's like having a super detailed record of
everything that happened leading up to the crime,
making it much easier to identify the culprit.
So it's like having a digital trail of breadcrumbs
leading right to the source of the problem.
Exactly.
And this level of detail is
essential for truly understanding and solving
those complex manufacturing problems.
It goes beyond just fixing the symptom
and allows you to address the root
cause, preventing it from happening again.
So it sounds like these MES systems are really
taking root cause analysis to the next level.
Absolutely.
the TME® MES System
Yes
What's so special about that one?
It's a great example of how these systems
are being tailored specifically for root cause analysis.
Okay.
It goes way beyond just basic data collection.
Imagine a scenario where a batch
of products fails a quality check.
Okay. Yeah.
TME® can instantly trace those faulty products back
to the exact machines and materials, even operators.
Oh, wow.
So it's like a detective that could retrace every step.
Exactly.
And then it takes it even further.
Generates reports, suggests potential root causes
based on all that data.
It can even flag similar incidents from the
past to help you identify recurring patterns.
So it's like taking Five Why's and 8D and giving them
a boost with all this data
and AI
that's mind blowing.
Yeah.
But all of this raises a question for me.
If we can predict and prevent these problems
before they even happen, what happens to the
need for, you know, the old ways?
Right.
Will Five Why's and 8D become obsolete in the future?
It's a really interesting question.
Yeah.
It makes you wonder if these technologies are going
to completely change how we approach problem solving.
Maybe it's not about replacing
those old methods entirely.
Yeah.
But finding ways to integrate them
with all these powerful new tools.
I think it's a great point.
It's not about picking one or the other
Exactly.
It's about finding the balance between human
expertise and this amazing new technology.
So we've gone from, like, Henry
Ford's really simple approach, you know,
just wanting to make things consistent.
Right.
All the way to AI that can, like,
almost predict the future on the factory floor.
It's pretty incredible.
It's mind blowing how much things have changed.
But I'm also curious, like, where do we go from here?
What does the future hold for root cause analysis?
Well, that's the big question, isn't it?
Yeah.
But what I'm really excited about is,
you know, we've talked about AI analyzing
all this data, spotting patterns.
Right.
But what if it goes beyond just
identifying, like, what the problem is?
Okay.
What if it can help us understand
WHY at a whole new level?
Okay, now you've got me really intrigued.
Like, give me an example.
What could AI uncover that we humans might miss?
Okay, so imagine an AI system that's been
keeping track of not just machine performance data,
but also things like employee schedules.
Okay.
Weather patterns, even tiny shifts in the supply chain.
Oh, wow.
It might find a link that we would never think of.
Like, let's say, how humidity spikes on certain
days are connected to a specific defect, even
though they seem totally unrelated to us.
Oh, wow.
So The AI isn't just like faster at
finding a needle in a haystack, it's finding
needles in haystacks we didn't even know existed.
Exactly.
That's incredible, but also kind of scary.
What if we become too reliant on these systems?
Like, what if we forget
how to solve problems ourselves?
That's a valid concern, and it's definitely
something we need to be careful of.
But I see it more as a way to
enhance our own abilities, not replace them entirely.
Think of AI as a powerful tool that can help
us see things from new perspectives, make connections we might
have missed, and become even better problem solvers.
That's a really interesting idea. It's exciting.
But it also makes me wonder about, like,
what are the unintended consequences of that?
Do we lose the ability to adapt to unexpected problems?
Do we become complacent?
Those are great questions, and to be honest,
we don't have all the answers yet.
But that's what makes this such a fascinating field.
It's not just about the technology, it's about us.
The human implications, the ethical questions.
We have to constantly adapt and learn.
Wow.
And this is just the beginning.
As technology continues to advance, we can expect
even more sophisticated tools and techniques to emerge,
making problem solving even more efficient and effective.
It's incredible to think about how far we've come.
We've gone from Henry Ford simplifying processes
to sophisticated systems that can practically predict
the future of a factory.
It's all about shifting your mindset.
Approaching problems with that same curiosity
and determination to uncover the why.
So for all of you listening, the next
time you're faced with a challenge
Ask yourself those whys.
Even if it feels a bit silly at first,
you might be surprised by what you uncover.
And who knows, maybe you'll even invent
the next big problem solving tool.
It's been an incredible journey exploring the world
of root cause analysis from those early assembly
lines to the high tech factories of today.
But one thing remains constant, that human drive to
understand the why behind things and make them better.
Absolutely.
So to all our listeners out there, keep
those minds curious, keep those questions coming, and
keep pushing the boundaries of problem solving.
You never know what amazing
solutions you might discover.
And until next time, keep on diving deep.
From Foundation to Future: How Root Cause Analysis Evolved
Root cause analysis has been central to manufacturing since the early 1900s, when Henry Ford's assembly line led him to simplify and standardize processes. Decades later, Toyota’s Five Whys brought a new layer of depth by uncovering problems’ root causes through simple, iterative questioning. Ford Motor Company then introduced the Eight Disciplines (8D) process to tackle more complex, team-based issues with a structured approach. Each method is a building block, leading to the sophisticated systems we use today.
The Five Whys: A Simple Yet Powerful Tool
Toyota's Five Whys method is a deceptively simple tool with profound impact. By asking “Why?” five times, teams dig past surface-level symptoms to uncover the core issue, peeling back each layer like an onion until they reach the root cause. This approach has empowered manufacturers to solve problems effectively without overcomplicating the process, making it a cornerstone of continuous improvement across industries.
The Eight Disciplines (8D): A Structured Approach to Complex Problems
Ford Motor Company’s Eight Disciplines (8D) process took root cause analysis to a new level, transforming it into a collaborative and structured methodology. With eight clear steps, 8D equips teams to tackle complex issues systematically, ensuring that problems are not only fixed but prevented from recurring. These steps are listed below:
D1: Establish the Team
Assemble a team with the necessary skills, knowledge, and authority to solve the problem. It’s crucial to bring together diverse perspectives to fully understand the issue and ensure comprehensive problem-solving.
-
D2: Define the Problem
Describe the issue in quantifiable terms to understand the scope and impact. A clear, specific problem statement helps the team stay focused and aligns everyone on what needs to be resolved. -
D3: Implement Interim Containment Actions
Take temporary actions to prevent the problem from affecting customers or processes while the root cause is identified. These short-term fixes safeguard quality and customer satisfaction while the team works on a long-term solution. -
D4: Identify Root Causes
Use analytical tools, such as the Five Whys, to uncover the root cause(s) of the problem. This discipline aims to dig deep, looking beyond surface issues to reveal the underlying factors driving the problem. -
D5: Develop Permanent Corrective Actions
Create solutions to address the root cause and prevent the issue from recurring. These corrective actions should be carefully designed to not only fix the problem but also enhance overall system reliability. -
D6: Implement and Validate Corrective Actions
Put the permanent corrective actions in place and confirm they resolve the issue effectively. Testing and validation ensure that the solution is sustainable and prevents unintended consequences. -
D7: Prevent Recurrence
Modify systems, procedures, or processes to ensure the problem does not happen again. Documenting the changes and updating standard practices helps the entire organization learn and benefit from the resolution. -
D8: Recognize the Team
Acknowledge the team's efforts and contributions to solving the problem. Celebrating success not only boosts morale but also reinforces a culture of continuous improvement and collaboration.
This enhanced 8D approach ensures a thorough resolution, from problem identification to preventive measures, creating a strong foundation for sustainable manufacturing excellence and is especially powerful in high-stakes manufacturing environments, where comprehensive solutions are critical to maintaining quality and efficiency.
Modern Tools for Root Cause Analysis
Today’s Manufacturing Execution Systems (MES), like MASS Group's TME® MES, elevate root cause analysis through real-time data, automation, and predictive insights. Imagine having a digital detective on the factory floor, constantly collecting and analyzing data to prevent issues before they occur. This episode explores how TME® MES leverages these principles to optimize problem-solving.
The Future of Problem Solving in Manufacturing
AI and automation promise to reshape manufacturing problem-solving. In this episode, we consider a future where AI might not only identify issues but predict and prevent them before they impact production. As root cause analysis continues to evolve, manufacturers are positioned to benefit from increasingly proactive, data-driven solutions.
Final Thoughts
With modern tools like MES systems, manufacturers gain real-time insights that deepen root cause analysis, helping teams to address issues before they impact production. As we look to the future, the goal remains the same: to use root cause analysis not only to fix what’s broken but to continually improve, innovate, and achieve manufacturing excellence.
Root cause analysis, in its many forms, is about more than troubleshooting—it’s about creating resilient systems that support continuous improvement. By combining human expertise with advanced technology, we’re building a future where manufacturers can anticipate, adapt, and thrive in an increasingly complex world.
Subscribe to The Root Cause Podcast on YouTube or follow MASS Group on LinkedIn for more insights into manufacturing, automation, and innovation. Stay tuned for more episodes that dive deep into the trends shaping the future of this exciting industry!