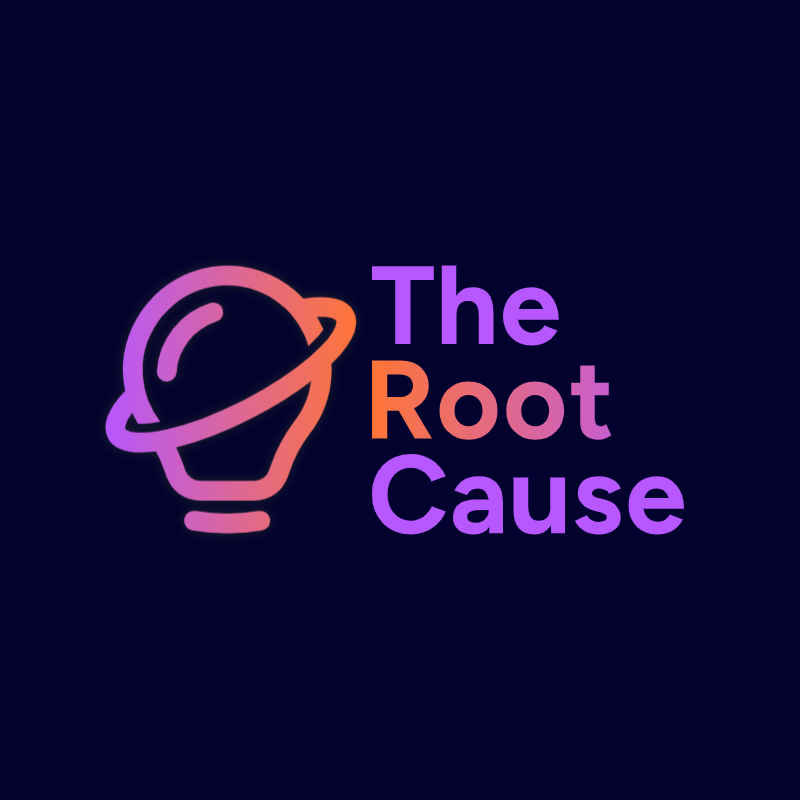
Ep. 8 MES vs. ERP: Understanding the Key Differences
The Root Cause Podcast Ep. 8 - Explaining the Differences between MES and ERP
Manufacturers are navigating an increasingly complex landscape, balancing operational efficiency with strategic decision-making. In this episode, we break down the essential differences between Manufacturing Execution Systems (MES) and Enterprise Resource Planning (ERP) systems, exploring how these two platforms complement each other to drive manufacturing excellence.
Drawing insights from real-world examples, this episode sheds light on the roles MES and ERP play in modern manufacturing, helping manufacturers understand when and how to use these systems effectively.
What We Cover in Episode 8:
- MES as the “factory floor translator,” turning machine data into insights
- ERP as the “strategic brain,” driving planning and financial decisions
- How MES and ERP integrate for seamless operations
- Real-world examples of MES in batch management, KPIs, and maintenance
- The future of convergence: Are MES and ERP merging into one system?
on what you already know about MES.
You know, that intricate dance
of managing the factory floor.
But today we're zooming out.
Okay.
To the bigger picture.
I like it.
Where ERP comes in.
Yeah.
And it's a whole different beast.
It is.
And understanding ERP can unlock
some serious aha moments.
Absolutely.
About how businesses really tick.
For sure.
MES and ERP.
What are the big differences and
how do they work together?
Okay, so picture this, okay?
A busy factory floor.
Machines are going, products are moving down the line.
Classic MES territory.
Got it. But then, zoom out.
You've got sales, finances, the whole operation.
That's ERP's domain.
Two massive systems.
But they're connected, right?
Absolutely.
So how does, like data from a single machine
on the floor, how does that make its way
up to, say, the CEO making big decisions?
That's the fascinating part.
MES and erp, they're kind of separate worlds.
But both, both are essential for
a manufacturing company to really succeed.
Gotta have both.
They operate at different levels of the hierarchy.
Think of it like you have individual
machines and processes at the base level.
Okay.
At the bottom, then you go up to the
plant level, and then finally the enterprise level.
MES is right in the middle, bridging the
gap between the physical production happening down on
the floor and all those digital business processes.
So MES is kind of translating all that raw data
from the machines into something that people can actually use.
Right.
That's a great way to put it.
It's like giving the factory floor a voice so
it can talk to the rest of the company.
Exactly.
And that communication is key, turning
all that data into action.
Right.
Got to do something with it.
Take for example, Statistical Process Control.
MES can gather real time data on,
say, temperature or pressure while products are being made
while it's all happening.
And if things start to go off even a
little bit, MES can instantly alert the operators.
They can make adjustments on the fly.
So you're catching problems before
they become big problems.
Exactly.
You could prevent a whole batch of
faulty products, save time and money.
That's huge.
It shows how MES's focus on real time data has a
direct impact on, you know, the bottom line for sure.
Now let's look at ERP.
It's the backbone of the enterprise, managing
everything from finances to supply chains.
It's like the brain of the operation
trying to make sense of all the
information coming from all the different departments.
An ERP needs accurate, real time
data to make good decisions. Right.
100%.
Things like resource allocation, planning,
production, even financial forecasting.
All of it.
You gotta have a clear picture of
what's happening down on the floor.
That's where the connection with
MES gets really important.
You need that constant flow
of information coming from MES.
That way, ERP's decisions are based
on reality, not just outdated assumptions.
Because otherwise, it's kind of operating in the dark.
Exactly.
Imagine your sales team just got a huge new order.
ERP needs to know if the
factory can even handle that demand.
Right.
Can we actually do it?
Right? Can we make it?
Do we have enough materials
with a realistic delivery time?
It's about using real time
data to make smart decisions.
And that's where MES comes in.
Exactly.
That level of insight is what allows
companies to be agile, to be responsive
in a world that's constantly changing.
It's about having your finger on
the pulse of your operations.
You know exactly what's happening at every level.
So let's look a little closer at how
this connection plays out on the factory floor.
One of the key functions of MES is batch management.
Batch management?
Yeah.
And this isn't just about, you know, tracking groups
of products as they move through the system.
It's really about making sure each
batch meets those specific quality standards.
Right.
Making sure it's all good and that.
It follows the right processes. The right recipe.
Like, think of it as a recipe.
Okay, A recipe.
MES makes sure all the ingredients are added
in the right order at the right time
to create that perfect final product.
So MES is like the digital
recipe book guiding the production process.
That's pretty cool.
Yeah.
But how does this all connect back to ERP?
Well, that's where the magic of integration comes in.
As MES is managing all these batches, it's constantly
feeding information back up to the ERP system.
Okay. Keeping it updated.
Right.
And that data includes things like the batch
size, the materials used, the production time.
Right.
And of course, all the quality control results.
Got to have that.
So ERP uses all this data to update
inventory levels, track production costs, even generate reports,
you know, for things like regulatory compliance.
Wow.
So it's not just about keeping
things organized down on the floor.
Nope.
It's about having this, like, comprehensive
view of the whole operation.
Right.
From raw materials to finished goods.
Exactly.
And that kind of visibility is crucial for making
informed decisions at every level of the company.
Yeah, you got to see the whole picture.
And it goes beyond just tracking batches.
MES also plays a crucial role in KPI optimization.
Okay.
KPI's key performance indicators. We hear that a lot.
Right.
And this is where you start to
see the real power of MES in
terms of driving efficiency and improving performance.
Think about a KPI,
like Overall Equipment Effectiveness. OEE.
Right, OEE Getting the most out of your machines.
Exactly.
Minimizing downtime.
You're finding those bottlenecks.
You're streamlining the process.
So how does MES fit into all of that?
Well, MES can collect real time data from the machines.
You know, things like their operating status, how
many units they're producing, any downtime events.
Right.
Keeping tabs on everything.
And then it uses all of that data to calculate
the OEE and identify areas where we can do better.
Maybe there's a particular machine that's consistently
underperforming, you know, having frequent breakdowns.
MES can highlight those issues.
So you can actually take action and fix it.
Exactly.
Allowing managers to take corrective action.
So MES isn't just watching.
It's actively helping to optimize production.
It's like having this constant feedback loop.
I like that.
Yeah, a feedback loop.
It's pinpointing those areas where
things can be improved.
You know, making those small adjustments that
end up having a big impact on
the efficiency of the whole factory.
It's all about the details.
And this ties directly back
to that connection with ERP.
When MES finds those areas for improvement, it can
send out alerts or notifications to the right people.
So for instance, if a machine needs maintenance,
MES can automatically generate a work order in
the ERP system, schedules the maintenance, and makes
sure the necessary parts are ordered.
That's great.
It's preventing those costly delays.
It's like using data to anticipate problems and then
take steps to solve them before they even happen.
Proactive.
Exactly.
Yeah.
But let's shift gears a little bit.
Let's talk about another key function. Maintenance.
Yeah.
MES plays a crucial role in shifting from
reactive maintenance to a more proactive approach.
So instead of just waiting for something to break down.
Right.
Putting out fires, MES uses real time
data to predict when maintenance is needed.
That's a much better approach.
So imagine you have a sensor on a
piece of equipment, a critical piece of equipment.
Okay.
And it's measuring vibration levels
as those vibrations increase.
It could mean that the equipment is wearing
down, you know, getting closer to failure.
Looks like an early warning system.
Exactly.
It helps prevent those catastrophic failures that
can shut down the whole production line.
Yeah, nobody wants that.
Right.
And MES takes it even further by integrating
with the ERP system to manage that entire
maintenance process so it can schedule maintenance tasks,
track spare parts, even generate reports on maintenance
costs and how the equipment's performing.
It's about having that one system where you
know everything is in tip top shape.
You've got it all covered. That's amazing.
How MES can turn all that raw data from
the floor into actionable insights that can improve everything
from efficiency to how long your equipment lasts.
It's pretty powerful.
But there's one more key function
we need to talk about.
Lab Information Systems.
LIMS.
Oh, yeah.
This is another area where MES plays
a crucial role, especially in those industries
with really strict quality control requirements.
Right.
Think pharmaceuticals, food processing.
Gotta be careful there.
They rely heavily on lab testing to make
sure their products are safe and high quality.
Absolutely.
Making sure everything meets the standards.
Right.
Making sure what's on the label
is actually what's in the product.
For sure.
So how does MES help with that?
Well, it acts as a bridge between
the laboratory and the production floor.
Okay. Connecting the two.
And make sure all the data from those quality
control tests is integrated into the whole production process.
So that includes things like tracking samples, test
results, any deviations from those quality standards.
So it's like creating a closed loop, right?
Exactly.
Any quality issues are flagged immediately, you.
Catch them right away.
So you prevent those faulty products from moving
down the line and maybe even reaching customers. Yeah.
Could I stop it early?
MES can even trigger automatic adjustments to the
production process if there's a quality problem.
So you're guaranteeing that only products that meet
the standards are going out the door?
It's all about control and traceability.
Right.
Building that trust and confidence in your product.
Okay, so we've Talked about how
MES manages batches, optimizes KPIs, streamlines
maintenance, and integrates with lab systems.
It's a powerful tool for really
fine tuning every aspect of production.
But how does all of this connect
back to that bigger picture of ERP?
Well, remember, the network is the
plumbing that connects MES and ERP.
It's the infrastructure that enables this constant
flow of information between the factory floor
and the rest of the enterprise.
Right.
It's all connected.
And we can't forget about
data security and system integration.
Absolutely crucial.
It's not just about the data flowing.
It needs to be secure, it needs to
be accurate, and it needs to be easily
accessible by the systems that need it.
Yeah, it's got to work.
That's why a robust and reliable network is
just as important as choosing the right MES
and ERP systems in the first place.
They all have to work together.
They got to work together seamlessly if you
want to truly optimize your manufacturing operations.
We've covered a lot of ground today from like
those individual machines working away to the big decisions
happening way up at the enterprise level.
Full ecosystem.
Yeah.
And it's clear that both MES
and erp, they're both critical.
First success in manufacturing.
But I'm curious, what's next?
What does the future hold for these systems?
The crystal ball question.
Well, one of the most interesting trends is
this increasing convergence of MES and ERP.
In the past, you know, they
were treated as totally separate things.
Two different worlds, almost like two
different languages struggling to communicate.
Right.
But now with technology advancing, those
lines are starting to blur.
Convergent.
So you're saying they're becoming more integrated?
Exactly.
Like two sides of the same coin.
Okay.
We're seeing software vendors offer solutions
that combine the best of both.
Imagine a single platform that can handle
everything from real time shop floor control.
Okay.
To enterprise wide planning and financials.
Wow, that makes a lot of sense.
Having everything in one system
would definitely simplify things.
Like all that data integration and communication.
It's about breaking down those silos
and having a truly connected enterprise.
I've learned a lot today.
I feel much more confident about
how MES and ERP work together.
And I'm excited to see where it all goes from here.
What's next in manufacturing?
Well, that's the beauty of it.
It's constantly evolving.
Stay curious, keep exploring, and who knows, maybe you'll
be the one to pioneer the next breakthrough.
That's a great note to end on.
Always learning, always exploring.
Thanks for joining us on this
Deep dives into MES and ERP. We'll catch you next time.
MES as the “Factory Floor Translator”
MES (Manufacturing Execution Systems) operates as the nerve center of the factory floor, transforming raw machine and production data into actionable insights. By connecting machines, sensors, and workflows, MES provides real-time visibility into production processes, allowing manufacturers to monitor performance, detect issues, and optimize operations. With MES, manufacturers can shift from reactive problem-solving to proactive decision-making, ensuring smoother workflows and better outcomes.
ERP as the “Strategic Brain”
ERP (Enterprise Resource Planning) systems serve as the strategic brain of the organization, coordinating high-level planning, financial management, and resource allocation across departments. ERP goes beyond the factory floor, integrating supply chain, inventory, HR, and financial operations into a unified system. This big-picture approach ensures long-term planning and resource optimization, enabling manufacturers to make informed decisions that align with business goals.
How MES and ERP Integrate for Seamless Operations
While MES manages the granular details of production, ERP provides the overarching strategy. Together, they create a seamless manufacturing ecosystem. MES collects and analyzes real-time production data, feeding insights into the ERP system, which uses this information to adjust inventory levels, update schedules, and refine resource planning. With the right resources, this integration can be seamless and ensures that both operational efficiency and strategic objectives are aligned, bridging the gap between shop floor execution and enterprise management.
Real-World Examples of MES in Action
MES systems are transforming manufacturing with their ability to manage batch production, optimize KPIs, and enhance maintenance. For example, MES tracks and ensures consistency in batch production, enabling manufacturers to meet strict quality standards. By monitoring KPIs like machine efficiency and downtime, MES provides actionable data to improve operations. Additionally, MES enables predictive maintenance by analyzing equipment data to prevent costly breakdowns, ensuring production remains uninterrupted.
The Future of Convergence: MES and ERP Merging into One System?
As manufacturing technology evolves, the lines between MES and ERP are beginning to blur. Emerging trends suggest a future where these systems converge, combining the real-time data capabilities of MES with the strategic insights of ERP into a unified platform. This convergence could unlock new levels of connectivity, allowing manufacturers to gain a holistic view of operations while maintaining the agility needed to adapt to industry changes. The question remains: will this evolution redefine how manufacturers manage their operations?
Final Thoughts
MES and ERP are essential tools for manufacturers looking to stay competitive. By understanding their unique strengths and integrating them effectively, organizations can achieve streamlined operations, improved efficiency, and data-driven decision-making.
At MASS Group, we specialize in helping manufacturers leverage these systems to create smarter, more connected workflows. Ready to transform your operations? Schedule a demo and see how we can help.
Subscribe to The Root Cause Podcast on YouTube or follow MASS Group on LinkedIn for more insights into manufacturing, automation, and innovation. Stay tuned for more episodes that dive deep into the trends shaping the future of this exciting industry!