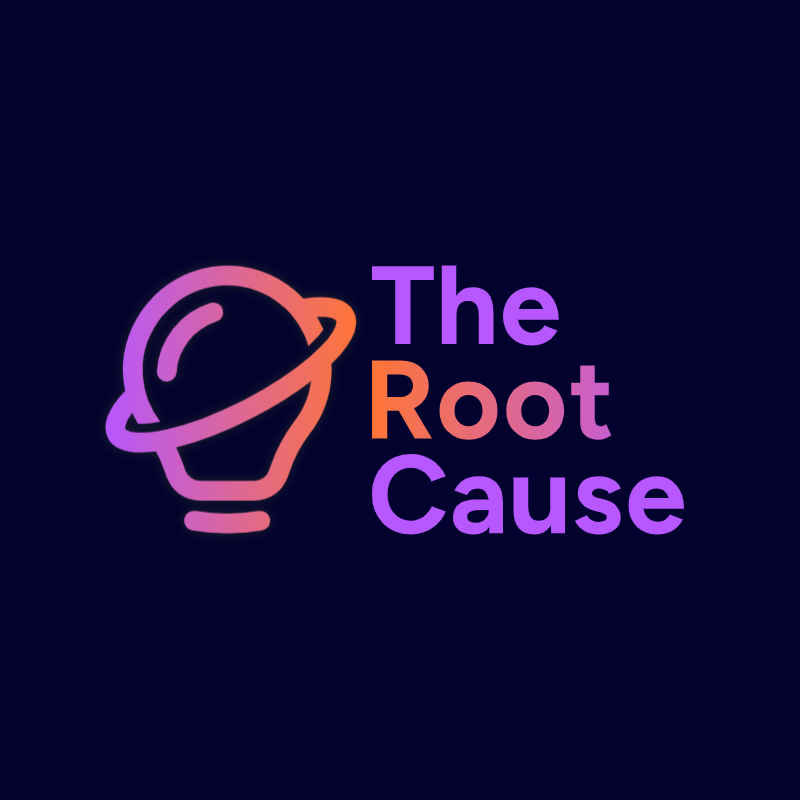
Ep. 17 What is CMMS and Why It's Critical to Modern Manufacturing Maintenance
The Root Cause Podcast Ep. 17 - What is CMMS and Why It's Critical to Modern Manufacturing Maintenance
In this episode of The Root Cause, we unpack what a CMMS (Computerized Maintenance Management System) actually is—and why it's become mission-critical for manufacturers looking to reduce downtime, extend asset life, and drive smarter maintenance strategies.
We also explore insights from Automation World’s recent article, Why CMMS Remains Critical to Manufacturing Maintenance, including next-level benefits like data-driven maintenance, embedded safety procedures, and full system integration.
[A: 00:07.9]
Okay, picture this. You're trying to keep everything running smoothly, maybe in a factory or a large facility, but it just feels like constant chaos. You know, like you fix one thing, another breaks down, work orders are just piling up. Maybe you're wrestling with these messy spreadsheets, trying to track everything manually.
[A: 00:24.1]
It's like you're playing a game you just can't win. Well, what if there was a way to swap that chaos for clarity? Today, we're doing a deep dive into something that promises just that. CMMS, that's Computerized Maintenance Management System. This is basically your shortcut to understanding how to turn those maintenance headaches into, well, something manageable.
[B: 00:45.3]
That scenario is, incredibly relatable for so many teams, especially today. Right. Budgets are tight. Sometimes workforces are smaller than they used to be. Getting reliability, keeping things running. It's not just nice to have, it's absolutely essential, particularly if you're manufacturing.
[B: 01:01.1]
And yeah, CMMS is really how organizations are starting to deliver that reliability.
[A: 01:05.6]
Alright, so let's unpack CMMS We've used the acronym, but what is it really? At its heart..
[B: 01:09.6]
fundamentally, it's software. software specifically designed to help maintenance teams get organized. It automates processes, it tracks all the maintenance activities. It really lets teams get ahead of problems instead of just reacting all the time.
[A: 01:22.8]
I like to think of it as, maybe like an extra team member. You know, one who never forgets a task, never loses a work order, and then definitely doesn't call in sick. It's about shifting from reactive to proactive.
[B: 01:35.9]
That's a great analogy, because before CMMS really took hold, it was chaotic. People were relying on, like you said, spreadsheets maybe whiteboards, stacks of paper even. And that inevitably meant things got missed. Tasks slipped through the cracks. You'd have those sudden unexpected breakdowns and then boom, expensive emergency repairs.
[A: 01:53.4]
Right.
[B: 01:53.8]
What CMMS does is it centralizes everything. All that information, all those tasks in one place. That streamlines the whole process, makes it way more efficient, and cuts down massively on human error.
[A: 02:04.8]
Okay, so it's the central hub, but how does it actually work day to day? What are the sort of key tools inside a CMMS that let companies actually get a grip on their maintenance?
[B: 02:15.3]
Yeah, good question. It breaks down into a few core functionalities. Think of it as the engine under the hood. First up, you've got asset management. This isn't just listing your equipment it tracks everything each asset, machines, vehicles, whatever. service history, warranty info, performance data, it logs it all this helps you spot potential issues.
[B: 02:36.8]
sometimes way before they become big problems.
[A: 02:38.7]
so it's like an early warning system for your equipment.
[B: 02:41.1]
Exactly. Then there's work order management. This is huge. It automates the creation and assignment of work orders. You can track progress easily set priorities Is this urgent? Can it wait? And make sure things actually get done on time?
[A: 02:54.3]
Takes away the paper shuffle totally.
[B: 02:56.2]
And linked to that is preventive maintenance scheduling. This is where you get proactive. You set up recurring tasks, inspections, lubrication, filter changes, whatever it is. The CMMS schedules them automatically which, you know, minimizes those surprise breakdowns and the big repair bills that come with them It's that whole ounce of prevention idea, but automated.
[A: 03:14.9]
Makes sense.
[B: 03:15.5]
Then you've got inventory control. You need spare parts for maintenance, right CMMS keeps track of what parts you use, how many you have left, and it can even automatically reorder supplies when you're running low. So no more delays because you're waiting on a crucial part.
[A: 03:28.2]
Okay. That's critical. Avoids downtime, just waiting for parts.
[B: 03:31.5]
Precisely. And finally, reporting and analytics. Because it tracks everything, the CMMS can generate really detailed reports. This lets managers see trends, understand costs, allocate resources better. Basically, make decisions based on actual data not just guesswork.
[B: 03:48.2]
It's about long term planning, too.
[A: 03:49.9]
Wow. Okay, that covers a lot of ground. It sounds incredibly useful for almost any operation that relies on physical assets. But let's zoom, in, especially for listeners in manufacturing, this is where it gets really interesting, right Why is CMMS not just helpful, but maybe even critical in a manufacturing environment?
[A: 04:06.6]
How does it directly boost that predictability and efficiency on the factory floor?
[B: 04:11.1]
Oh, absolutely. In manufacturing, the stakes are often higher. The impact is, well, profound. Let's dig into some specific benefits there. Number one is reducing equipment downtime. This is massive. When a key piece of machinery goes down unexpectedly in a factory, production stops.
[B: 04:27.4]
The costs can be astronomical. There are estimates like up to $50 billion a year lost by industrial manufacturers just due to downtime.
[A: 04:35.1]
50 billion. Wow.
[B: 04:36.4]
Yeah. CMMS fights this directly by automating preventive maintenance, by flagging potential issues early based on asset data. It means fewer surprises, smoother workflows, less disruption. It's moving from firefighting to fire prevention.
[A: 04:49.3]
Okay, that financial hit alone makes a strong case. What else?
[B: 04:52.6]
Improving work order efficiency think about the old way, maybe a vague note on a work order form, if you can even find the form. Trying to figure out what needs doing, tracking down the technician. CMMS cleans all that up. It generates precise, detailed work orders, often automatically triggered by schedules or asset conditions.
[B: 05:09.9]
Technicians can get these on mobile devices, update the status in real time and every single action gets logged digitally. You have a complete history. Nothing gets lost.
[A: 05:19.3]
So better communication, better tracking. Got it.
[B: 05:21.6]
Then extending asset lifespan. Replacing major industrial equipment is incredibly expensive. As you know, a CMMS helps you maximize the life of your current assets through proper, consistent maintenance. Those scheduled inspections, lubrications, timely part replacements, they all add up.
[B: 05:37.9]
Companies using CMMS often report like a 20% or even greater increase in how long their key equipment lasts, plus fewer catastrophic failures. It's just smart asset management.
[A: 05:47.6]
20% longer life, that's a significant saving on capital expenditure right there.
[B: 05:52.3]
Absolutely. And that ties into the next point. Cutting maintenance costs overall, when you're always reacting, paying for emergency repairs, maybe overtime, labor rush, shipping for parts. It's expensive. CMMS helps you shift to that preventive model, which is inherently cheaper. Catching small problems before they become big, costly ones.
[B: 06:10.6]
We see reports of maintenance cost reductions of up to 30%.
[A: 06:13.5]
30% reduction, that's substantial.
[B: 06:15.8]
It really is.
[A: 06:16.4]
Yeah.
[B: 06:16.7]
And another powerful aspect is data driven decision making. Because the CMMS logs everything. Every task, every part, every hour spent, every breakdown. You build this incredible database. You can finally see clear trends. Why does this machine break down more often? Are we spending too much on that type of repair?
[B: 06:32.7]
You can answer budget questions with hard data, justify staffing levels. It turns maintenance data into actionable intelligence.
[A: 06:38.9]
So it takes the data guesswork out of planning and budgeting.
[B: 06:41.9]
Exactly. And don't forget optimized inventory management. We touched on it. But tracking spare parts accurately, automating reorders before you run out. This avoids holding too much costly inventory and avoids the production halts caused by not having a part when you need it. It's a balancing act that CMMS manages really well.
[A: 06:59.2]
Right? Finding that sweet spot for inventory.
[B: 07:01.8]
One last point particularly crucial in manufacturing monitoring regulation compliance. Many manufacturers face really strict safety or environmental regulations. CMMS is a huge help here. It keeps those comprehensive maintenance logs automatically proof that you're doing what's required.
[B: 07:17.7]
It can schedule mandatory inspections, send reminders, even generate reports formatted specifically for audits. It makes staying compliant much, much easier.
[A: 07:26.1]
Okay, that compliance piece is critical. Avoiding fines, ensuring safety. Yeah. So that $50 billion downtime figure, the potential 30% cost savings. It really paints a picture. It sounds like CMMS isn't just organizing maintenance. It's turning it into a strategic lever for the business.
[A: 07:43.6]
And this actually connects really well to some more advanced ideas I saw in an Automation World article. It was called Why CMMS Remains Critical to Manufacturing Maintenance It talked about how CMMS delivers reliability through like strategic data use, automating safety checks and integrating with other systems.
[B: 07:59.6]
Yes, that's a great article. Michael Mills from Fluke Reliability makes some excellent points there. What's fascinating is how he breaks down these sort of next level impacts. He talks about data driven maintenance, for instance. He emphasizes how CMMS really becomes the central hub for all plant activities, especially for predictive maintenance.
[B: 08:18.2]
So imagine a sensor on a machine detects high vibration. That alert doesn't just flash a light, it can trigger the CMMS. The CMMS then pulls together everything needed. The asset's health history, past work orders, maybe even lists the parts and tools required for inspection. It can even auto generate a work order based on data from say a SCADA system or a building management system.
[A: 08:38.6]
So it connects the dots automatically, from sensor alert to maintenance action.
[B: 08:43.1]
Precisely. It closes that loop incredibly quickly, moving you from just reacting to predicting and preventing failures based on real time conditions. Then there's the automating safety aspect he mentions. Now, a CMMS can't physically lock out a machine, obviously, but its workflow engine can be set up to embed safety procedures right into the work order itself.
[B: 09:04.7]
For electrical work, for example, it could mandate steps like verifying power is off before the work begins. The system knows the potential risks associated with a task or asset and automatically includes the necessary safety precautions, Links to manuals, step by step guides, and crucially, he notes, the mobile aspect.
[B: 09:22.6]
Technicians can access this safety info right there, even offline.
[A: 09:26.0]
So it builds safety checks right into the workflow, making them harder to miss.
[B: 09:30.0]
Exactly. It helps standardize safety, reduces human error in potentially dangerous situations. It's like having a digital safety checklist for every job. And the third point from that article was integration. This is really key for modern CMMs. It's about its ability to talk to other systems.
[B: 09:46.7]
Think about integrating with SCADA for production data, ERP systems for inventory and purchasing, maybe even building management systems. This breaks down those data silos. CMMS gets a broader view, allowing for smarter maintenance prioritization based on production needs.
[B: 10:01.9]
For example, integration with, say, business intelligence tools helps with deeper analysis. Integration with ERP drives smarter inventory decisions, maybe tracking costs better. Even integrating with communication tools like Slack or Outlook helps connect teams.
[A: 10:17.1]
So it's not just an island of maintenance data. It becomes part of the bigger operational picture.
[B: 10:22.0]
That's the goal. A truly integrated CMMS shares data back and forth, making the whole operation more efficient and informed.
[A: 10:29.2]
Okay, this paints a really comprehensive picture from basic organization to These advanced integrated strategies, CMMS seems incredibly powerful. So bringing this back to a practical level for you, listening, maybe you're thinking, okay, I get it. We really need something like this. Where do you start?
[A: 10:45.1]
What does the solution look like? Let's maybe touch on a specific example like MASS Group's TME® CMMS. How does something like that fit into this picture?
[B: 10:53.5]
TME® is a specifically designed for manufacturers who need more than just basic tracking. It gives you that complete Visibility, work orders, asset health, even tracking subcontractor service activities. It's all in one central system. It has features like an ad hoc task library, automated alerts, and it uses spc, that's statistical process control data, to actually trigger work orders.
[B: 11:14.0]
So maintenance based on real process data.
[A: 11:16.4]
Okay, SPC driven work orders. That sounds advanced.
[B: 11:19.5]
It is. But here's the crucial part, especially based on what the source material highlights about TME® It's ease of implementation and use. This is key. It's designed to empower teams to get control of equipment uptime without getting bogged down in complex spreadsheets or needing to do custom scripting or programming.
[B: 11:38.0]
That often becomes a barrier with some systems. The complexity. TME® aims to avoid that. Making it faster to get up and running and actually used by the team.
[A: 11:46.8]
No scripting, no programming. That sounds like a big plus for teams that don't have dedicated IT resources just for maintenance software.
[B: 11:53.2]
Exactly. There's It doesn't try to overcomplicate maintenance. It gives you the structure you need, but also the flexibility. Flexibility to assign tasks quickly, track contractor work securely, trigger actions based on that real SPC data It's built for teams who frankly don't have time for guesswork or overly complex tools.
[B: 12:11.0]
It delivers the power without the typical implementation pain.
[A: 12:13.8]
So, structure plus flexibility. Easy to use, designed for manufacturers. That clarifies how a specific solution addresses these needs. So let's try and wrap this up. What's the main takeaway here? CMMS It's clearly not just another piece of software to add to the pile.
[B: 12:29.5]
Not at all.
[A: 12:30.1]
It really feels like the backbone of efficient modern maintenance. It's about keeping things running smoothly. Yeah. But also cutting those unnecessary costs, avoiding those painful breakdowns. It seems to genuinely transform those constant maintenance headaches into predictable, manageable workflows.
[A: 12:47.1]
It gives you back control.
[B: 12:48.5]
Absolutely. And maybe a final thought, or rather a question for you to consider. How can embracing a CMMS like this fundamentally change how your organization operates? Could it shift your team from being constantly reactive, always putting out the next fire to being more strategic, more forward thinking freeing them up to innovate, perhaps instead of just dealing with the latest crisis?
[A: 13:08.2]
And on that note, I think it's time to wrap up our deep dive Thanks for joining us, and we'll see you next time.
Read the full article from Automation World here.
Subscribe to The Root Cause Podcast on YouTube or follow MASS Group on LinkedIn for more insights into manufacturing, automation, and innovation. Stay tuned for more episodes that dive deep into the trends shaping the future of this exciting industry!