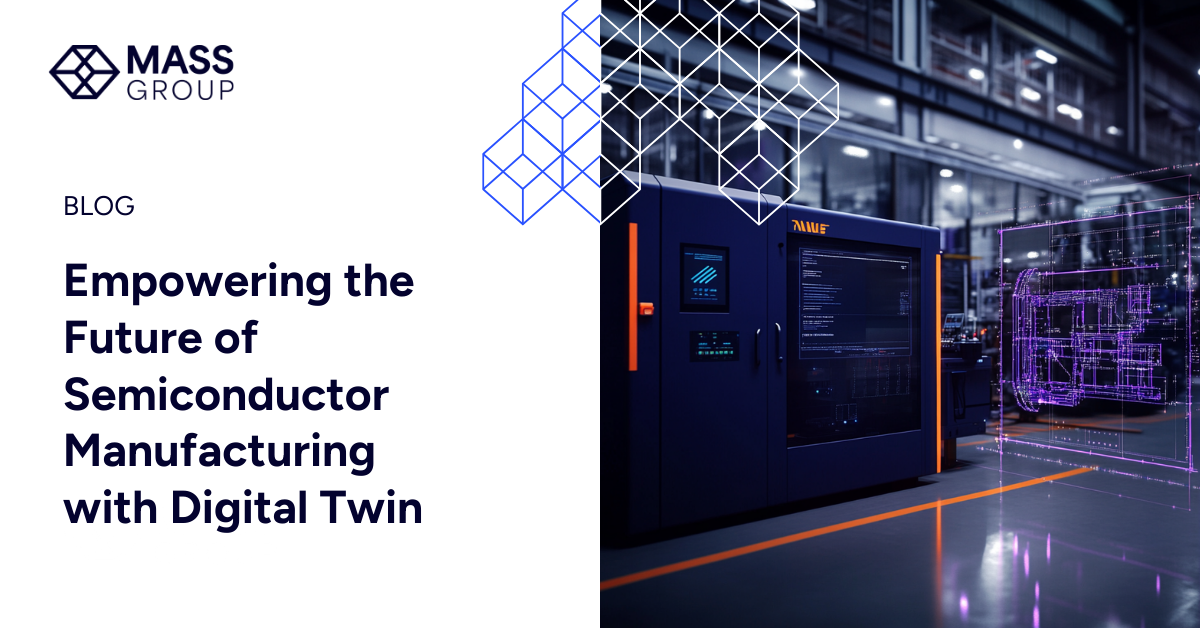
Empowering the Future of Semiconductor Manufacturing with Digital Twin
Leading semiconductor manufacturers are developing outsized advantages by actively improving their product development capabilities.
Their goal?
To shorten design and manufacturing cycles and reduce the expense of research and development.
Fractional production imprecision, material waste, and product delays can come with a considerable cost, not only in time and dollars but also in reputation and progress. Digitization is the key to win.
Semiconductor manufacturers are building on advances in computing power, analytics approaches, and artificial intelligence. This is the future of digital manufacturing. Process intelligence tools, process simulation software, and digital twin technologies are essential for solving complex production problems and fulfilling the promise of the U.S. CHIPS and Science Act.
A McKinsey & Company report indicated that almost 75 percent of companies in advanced industries, such as aerospace and automotive, have adopted digital twin technologies that have achieved at least medium levels of complexity.
This guide is designed to help manufacturers visualize how digital twin technologies accelerate product development processes, improve outcomes, and reduce costs.
Unlock Better Process Optimization with Digital Twins
The digital twin is a key capability for forward-thinking semiconductor manufacturers.
Under the CHIPS Act, the U.S. government has committed $285 million to advance digital twin technology in semiconductor manufacturing.
These virtual replicas of a real-world asset or environment helps manufacturers contextualize and anticipate their customers’ needs more efficiently than via direct observation. Manufacturers can use digital twins to model, test, and adjust prototypes and processes based on real data.
In manufacturing, they can represent every aspect of a product’s life, from design to in-use performance, including the processes employed to manufacture the product. It not only allows manufacturers to produce higher quality costs at a lower cost, but it also forms the backbone for new technology.
Digital twins process and react to various stimuli, which are data representing the external environment. They combine several models and they process data from multiple sources to simulate, predict, and optimize products and production systems before companies invest in physical prototypes and assets.
Digital twins provide valuable foresight prior to production as well as insights that drive continuous manufacturing improvements, like:
- Speed-to-market by seamlessly connecting the dialogue between design and production to accelerate tasks across all departments
- Reduced risks to company reputation by improving quality and real-time performance feedback across production
- Better margins by fully employing the virtual realm before investing in actual production
- Industry leadership by creating innovation efficiencies and continuous improvement
Common Challenges with Digital Twins and How to Overcome Them
Building a digital twin platform doesn’t happen with the flick of a switch. There are inherent challenges with integrating digital twin technologies into existing digital product development environments and wider IT infrastructure.
Digital twins require new ways of working, both within research and development functions and beyond them. That means a successful digital twin program is a change management effort that requires senior management’s commitment and support and a strong program management team to track milestones, develop new processes, and support adoption by the organization.
To overcome these potential roadblocks, manufacturers must consider various factors, including integration, scalability, support, customization, security, and cost. A best practice is to adopt a multi-phased approach to digital twin adoption.
Phase 1: Competitive intelligence and scoping
Identify the types of digital twin solutions available in a specific sector and estimate the potential value offered by each type. This work will also help organizations develop a framework for their transformation journey.
Phase 2: Architecture design and software stack
Identify the specific software components, relationships, and interfaces needed to meet digital twin ambitions. Design a software stack that provides the relevant capabilities, using a combination of existing tools and new elements, and decide whether those elements should be developed in-house or acquired from an external vendor.
Phase 3: Software-development-excellence
Develop the processes and capabilities needed to develop, integrate, and launch digital twin platforms.
Subsequent phases focus on the organizational transformation required to support new processes and working practices.
Improved Communication for Faster Innovation and Better Speed-to-Market
Innovation requires speed.
For a competitive advantage, manufacturers need to introduce and iterate innovative designs, materials and processes to their semiconductor manufacturing on an almost continuous basis, and at a rapid pace.
But speed carries risk, and risk in semiconductor manufacturing can lead to expensive waste.
How can introducing new innovations bolster—and not disrupt—product and process performance?
The key is tighter collaboration between product design and production, enabled by the digital twin. It gives businesses seamless connectivity to speed the dialogue across design and production so teams can:
- Operate in a common digital ecosystem and share a common data infrastructure, so design and manufacturing engineers are empowered to collaborate directly
- Enable product designers to consider manufacturing options before committing to a particular design
- Allow manufacturing engineers to study complex digital versions of product designs early in the development cycle to ensure they can be manufactured efficiently
- Share feedback between product design and manufacturing teams
- Streamline change management, enabling more agile processes
- Create a unified knowledge base built on a shared data backbone
High-Quality Feedback for Improved Performance and Reputation
A digital twin enables accountability and quality for every phase of the product development cycle. It can provide a virtual mockup of chip components, helping accurately simulate and validate its performance under various factory conditions so that high-quality semiconductor components are engineered, and later, plan and schedule assembly.
The digital twin is fundamental to resolving any issues that may arise during production or late stage development; and by catching errors sooner, teams can reduce risk and costly change. With timely collaboration between design, operations, production, and business systems, the digital twin helps manufacturers across a range of functions, including:
- Accurately verify resource availability, capability, and capacity prior to production
- Perform virtual validations that identify and inform cost-effective resolutions
- Proactively consider engineering or supply chain changes
- Use closed-loop insights from production to perform virtual analysis of recurring issues
- Perform corrective actions and impact analysis to incorporate changes in production
Pre-Production Digital Visualization for Better Margins
Improving margins relies on improving both product quality and production efficiency, which is exactly where the digital twin shines.
Increased demand for semiconductors is creating an evolution in product and process variations. Meanwhile, global and local manufacturing requirements and supply chain dynamics multiply complexity. Proactively managing these variables and achieving manufacturing excellence relies on visibility and control across the entire production process.
The digital twin enables semiconductor manufacturers to digitally connect engineering, operations, and the performance of plant resources with enterprise and automation systems to achieve better margins.
A digital twin enables:
- Optimal performance of operations with closed-loop collaboration
- Decreased cost of change and quality by synchronizing product, process, plant/asset and supply chain changes
- Accelerated innovations while maintaining the highest quality and operational efficiencies
- Establishment of a digital process for continuous improvement
- Corrective actions and impact analysis for error-proof incorporation of changes to production
Secure Industry Leadership with a Continuous Improvement Strategy
Digitization is profoundly changing the world for the better. Progressive manufacturers are already using digital tools but recognize the need for a more comprehensive approach to meet the demands of U.S. semiconductors and maintain U.S. technological leadership.
A sophisticated digital twin solution connects entire organizations seamlessly to enable two key capabilities: Complete visibility and control throughout the production process and a data-driven approach to achieve production excellence in fluid market conditions. This technology helps to remove the guesswork and better predict what will happen, improving responses to real-time trends both within the organization and in the market.
How MASS Group Supports Digital Transformation in Manufacturing
Digitization promises—and is delivering—the means for manufacturers to meet the demand for U.S. semiconductors. They must overcome disruptive influences through real-time, digital tools and dashboards that provide visibility into global operations. MASS Group supports the future of semiconductor manufacturing with real-time production tracking, control, and analysis.
Semiconductor manufacturing is a complex endeavor, and today's landscape presents unique hurdles.
As the industry approaches the limits of wafer size increases and chip miniaturization, manufacturers must find new ways to boost productivity and innovation. Digital twins are emerging as a crucial tool in the high-stakes semiconductor manufacturing environment to stay competitive and meet growing demand.
For semiconductor manufacturers looking to enhance their operational efficiency, improve product quality, and maintain a competitive edge in a dynamic market, implementing or upgrading to a state-of-the-art platform is not just an option—it's a necessity. Talk to one of our experts and see what MASS Group can do for you.