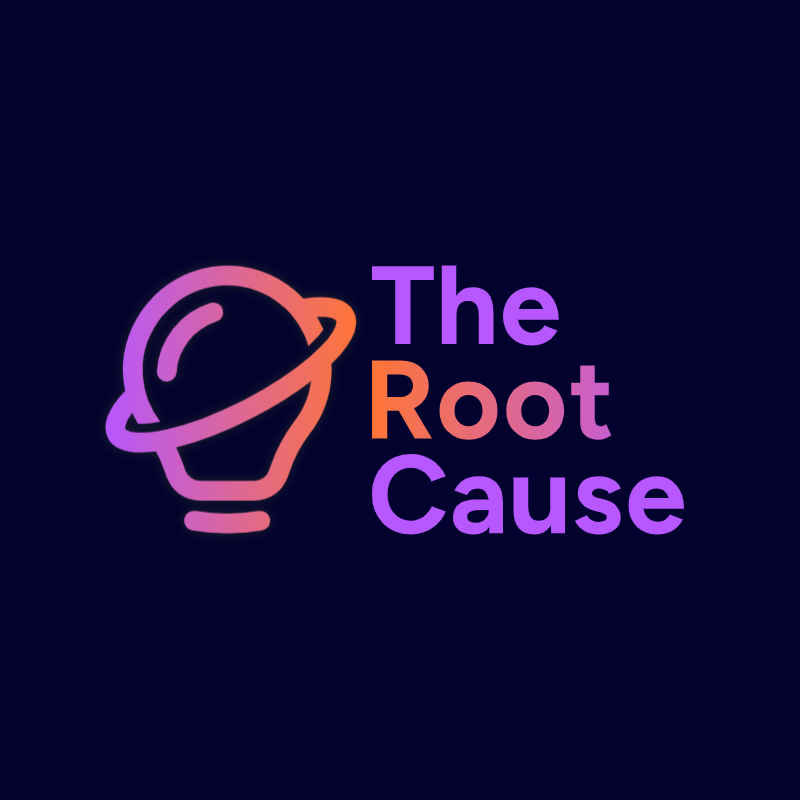
Ep. 10 Defect Tracking & Wafer Mapping to Optimize Semiconductor Operations
The Root Cause Podcast Ep. 10 - Integrating Defect Tracking & Wafer Mapping to Optimize Semiconductor Operations
Welcome to Episode 10 of The Root Cause Podcast! This episode focuses on the latest release of TME® software, designed to address the evolving needs of semiconductor manufacturers. With this update, MASS Group introduces a range of practical enhancements aimed at improving precision, efficiency, and usability for manufacturers navigating complex production environments.
This release highlights significant improvements, including customizable defect tracking, real-time wafer mapping, and seamless integration tools that streamline data management. These features empower manufacturers to address defects faster, optimize processes, and enhance overall operational efficiency.
What We Address in Episode 10:
- Customizable defect libraries for tailored problem-solving
- Real-time defect pattern visualization with heat maps and Pareto charts
- Wafer mapping for granular root cause analysis
- The integration of a defect collection API for seamless data centralization
- How these tools empower proactive manufacturing strategies
Welcome back, everybody. Today's deep dive is going to be pretty interesting. I think we're looking at MASS Group, and they make really great software for the semiconductor industry.
[B: 00:17.9]
Yeah.
[A: 00:18.4]
And so they just came out with a new update that has a bunch of really cool new features, and that's what we're going to be looking at today.
[B: 00:23.6]
I'm excited.
[A: 00:24.9]
But, you know, we're not going to get too bogged down in the technical details. Right. We want to really focus on the why behind these updates.
[B: 00:32.3]
Yeah, absolutely.
[A: 00:33.3]
And how they can benefit semiconductor manufacturers moving forward.
[B: 00:36.4]
For sure. I think one of the most fascinating things about this update is how it addresses, like, a fundamental challenge in the industry.
[A: 00:43.1]
Okay.
[B: 00:43.7]
And that's the. Just the sheer precision required in semiconductor manufacturing. You know, these chips are in everything these days.
[A: 00:52.6]
Everything.
[B: 00:53.3]
But even the tiniest imperfections can have a huge impact on their performance and yield.
[A: 00:59.0]
Yeah. It's crazy how something so small can cause such big problems.
[B: 01:02.7]
It really is. It's like a domino effect, but on a microscopic level.
[A: 01:06.4]
Exactly. And MASS Group seems to really understand that with these new features.
[B: 01:10.2]
Oh, yeah.
[A: 01:11.0]
Especially the enhanced defect and wafer mapping in their TME® software.
[B: 01:15.6]
That's a really smart move because it tackles a major pain point for manufacturers.
[A: 01:20.4]
Yeah.
[B: 01:20.9]
You know, traditional systems for tracking defects can be really rigid.
[A: 01:24.8]
Oh, okay.
[B: 01:25.4]
It's almost like trying to fit square pegs into round holes.
[A: 01:28.3]
Yeah, I can see that.
[B: 01:29.3]
But MASS Group takes a totally different approach. They're giving manufacturers the power to, like, define their own defect categories with a customizable library. So it's like going from off the rack clothing.
[A: 01:42.4]
Oh. Like that.
[B: 01:43.0]
To a perfectly tailored suit.
[A: 01:44.9]
That's a great analogy. So instead of being stuck with these, like, generic defect categories.
[B: 01:50.0]
Right.
[A: 01:50.5]
That might not really capture all the specifics of their processes.
[B: 01:53.5]
Exactly.
[A: 01:54.1]
Manufacturers can now create a library that's, like, perfectly tailored to their needs.
[B: 01:59.3]
Yeah. And that's so important in the semiconductor industry, where precision and continuous improvement are everything. This level of customization allows manufacturers to get really granular with their data.
[A: 02:11.0]
Okay.
[B: 02:11.5]
So they can capture and analyze even the tiniest variations that could affect yield and performance.
[A: 02:17.7]
And I noticed in the source material they mentioned something about being able to spot defect patterns across batches in real time.
[B: 02:23.8]
Oh, yeah.
[A: 02:24.8]
Is that as big a deal as it sounds?
[B: 02:26.7]
That is a game changer.
[A: 02:28.2]
Okay.
[B: 02:28.8]
Think about it. You're a manufacturer trying to figure out where this recurring defect is coming from. In the past, you might have spent days or even weeks sifting through spreadsheets and reports just trying to connect the dots.
[A: 02:40.7]
Ugh, that sounds awful.
[B: 02:42.2]
It was a nightmare. But MASS Group has addressed that with this update.
[A: 02:46.4]
Okay.
[B: 02:46.8]
They've introduced these dynamic visualizations heat maps and Pareto charts, Visual representations of data that help you quickly identify patterns and trends. It's like going from reading a black and white manual to watching a high definition movie.
[A: 03:01.9]
Okay, so you're trading a jumbled mess of numbers for a clear visual representation where you can actually see where these defects are clustering.
[B: 03:09.9]
Exactly. And that makes it so much easier to pinpoint the root cause of the problem.
[A: 03:15.0]
And because this analysis can happen in real time.
[B: 03:17.9]
Yeah.
[A: 03:18.5]
Manufacturers can take action much faster.
[B: 03:21.0]
Absolutely.
[A: 03:21.5]
Right. So they can prevent these small issues from snowballing into major production headaches.
[B: 03:27.5]
It's huge. Especially in an industry where time is money and any delay can be incredibly costly.
[A: 03:33.6]
So it's kind of like having a superpowered microscope.
[B: 03:36.0]
I like that.
[A: 03:36.8]
That not only magnifies the problem, but also points you directly to the solution.
[B: 03:40.9]
Exactly. It's about shifting from a reactive approach to a proactive one.
[A: 03:45.2]
I see.
[B: 03:45.8]
So instead of just putting out fires, you're preventing them from starting in the first place.
[A: 03:49.7]
And that's gotta be a huge relief for manufacturers.
[B: 03:52.2]
It is.
[A: 03:53.0]
Knowing that they have the tools to stay ahead of the curve and maintain that level of precision.
[B: 03:57.8]
Absolutely.
[A: 03:58.6]
That's essential in this industry, for sure. Okay, so we've talked about the big picture a little bit. Let's dive into the details now. I'm curious about the TME 7.5.4 release notes. Yeah, there's a lot in here. There is a whole bunch of updates and improvements.
[A: 04:17.1]
What are some of the things that stood out to you?
[B: 04:20.0]
Well, they've really focused on giving users richer ways to analyze their data.
[A: 04:25.5]
Okay.
[B: 04:25.9]
There are tons of new charts and gadgets you can add to your TME dashboards.
[A: 04:30.5]
More than just your standard, like bar charts and things like that?
[B: 04:33.9]
Oh, yeah, you've got your bar charts, but they've added more specialized options like scatter plots and even waterfall charts.
[A: 04:40.2]
Okay, but I mean, what does that actually mean for someone using this software every day?
[B: 04:44.2]
Right.
[A: 04:44.6]
How do these new charts actually help them understand their production processes better?
[B: 04:47.9]
Okay, so let's take the waterfall chart as an example. Okay. Great chart for visualizing the cumulative effect of different factors on a final outcome. So in the context of semiconductor manufacturing, this could help a production manager pinpoint exactly where yield losses are happening during fabrication.
[A: 05:05.2]
Interesting.
[B: 05:05.7]
It's like breaking down a complex recipe step by step.
[A: 05:09.4]
Oh, I see.
[B: 05:10.0]
To understand how each ingredient contributes to the final dish.
[A: 05:14.2]
So instead of just seeing the end result.
[B: 05:16.3]
Right.
[A: 05:16.8]
You can trace the entire journey.
[B: 05:18.6]
Yeah.
[A: 05:19.2]
And see exactly where things might be going wrong.
[B: 05:21.5]
Exactly. And. And that's the kind of insight that allows manufacturers to fine tune their processes and really squeeze every ounce of efficiency out of their operations.
[A: 05:31.8]
It makes a lot of sense.
[B: 05:32.8]
Yeah.
[A: 05:33.4]
Now, I also saw that they've enhanced their defect collection capabilities.
[B: 05:37.6]
Yes.
[A: 05:38.4]
Besides that customizable defect library we talked about, they've added wafer map rendering for a more interactive defect review.
[B: 05:46.5]
This is a fantastic addition because it goes beyond just logging a defect. It actually lets you see exactly where that defect occurred on the wafer.
[A: 05:54.9]
Oh, so it's like a visual map.
[B: 05:56.8]
It is.
[A: 05:57.4]
That highlights the problem areas.
[B: 05:59.0]
Exactly. Imagine a map highlighting hotspots for traffic accidents, but for defects on a semiconductor wafer.
[A: 06:04.8]
Gotcha.
[B: 06:05.5]
So now those defects have a location.
[A: 06:07.8]
Right.
[B: 06:08.3]
A context that can provide valuable clues for root cause analysis.
[A: 06:12.9]
It's like putting together a puzzle.
[B: 06:14.8]
Yes.
[A: 06:15.2]
Where each defect is a piece.
[B: 06:17.1]
Exactly. The more pieces you have and the more clearly you can see how they fit together, the better your chances of solving the puzzle.
[A: 06:24.5]
And that's exactly what this wafer map rendering feature does. It allows manufacturers to zoom in and out.
[B: 06:32.4]
Wow.
[A: 06:32.9]
Filter by different criteria, and really get a granular understanding of how defects are distributed across the wafer.
[B: 06:40.1]
That's pretty impressive.
[A: 06:41.2]
It is.
[B: 06:42.1]
Now, there's one thing I wanted to ask about, because I saw it in the release notes, but I'm not really sure what it means.
[A: 06:47.0]
Okay.
[B: 06:47.5]
They mentioned a new defect collection API.
[A: 06:51.1]
Oh, yeah.
[B: 06:51.8]
Can you explain what that is?
[A: 06:53.0]
Sure. An API or application programming interface is essentially a way for different software systems to talk to each other.
[B: 07:00.1]
Okay.
[A: 07:00.5]
So in this case, this new API allows manufacturers to seamlessly integrate data from their different pieces of equipment directly into tme.
[B: 07:08.9]
So it's like creating a central hub for all their production data.
[A: 07:12.4]
Exactly. Instead of having it scattered across different systems. So no more manually transferring data or trying to piece together information from different sources.
[B: 07:21.3]
Exactly. The API streamlines the whole data collection production process, which makes it much easier to get that holistic view of the entire production process.
[A: 07:31.3]
Okay, so, but how does that actually benefit manufacturers? I mean, what's the practical advantage of that?
[B: 07:36.8]
Well, think about it like this. Imagine trying to diagnose a medical condition by only looking at one symptom.
[A: 07:42.9]
Okay.
[B: 07:43.6]
You're probably gonna miss the bigger picture, right? Right. But if you can gather data from multiple sources, like blood tests, imaging scans, the patient's history, you have a much better chance of making an accurate diagnosis.
[A: 07:56.0]
So it's like having a complete medical record for your entire production process.
[B: 07:59.4]
Exactly.
[A: 08:00.0]
That allows you to see patterns and trends that you might miss if you were just looking at data in isolation.
[B: 08:05.1]
And that's the power of this API. It gives manufacturers those deeper insights so they can make more informed decisions and ultimately optimize their processes for maximum efficiency and quality.
[A: 08:16.3]
Yeah, for sure. One thing I saw was that they made some enhancements to the sales orders and WIP modules.
[B: 08:24.3]
Yeah.
[A: 08:24.6]
Can you tell me a little bit more about those?
[B: 08:26.1]
Sure. So now you can automatically create multiple work orders from a single sales order line item before you had to manually enter all those details, which was really time consuming and could lead to errors.
[A: 08:38.6]
Yeah, that sounds like a pain.
[B: 08:40.3]
So this new feature just makes the whole process much faster and more efficient.
[A: 08:44.3]
I like it. It's all about saving time and reducing errors.
[B: 08:47.1]
Exactly.
[A: 08:48.1]
What about the updates to the Sandbox and data import tools?
[B: 08:51.4]
Oh, yeah.
[A: 08:52.1]
Those seem to be more geared towards, like, the technical users.
[B: 08:54.7]
Yeah, those updates are all about making it easier for companies to scale their use of TME® and really configure it to their specific needs. The sandbox tool is great because it lets you test out changes in a safe environment before you actually roll them out to the live system.
[A: 09:09.7]
Like a dress rehearsal.
[B: 09:10.8]
Exactly.
[A: 09:11.3]
Before the big show.
[B: 09:12.3]
Yeah. You don't want to be making changes to your production systems without making sure that they're actually going to work, especially.
[A: 09:18.2]
In an industry like this.
[B: 09:19.3]
Oh, absolutely. The stakes are way too high.
[A: 09:21.7]
Right. Where any downtime can be incredibly costly.
[B: 09:24.8]
Exactly. So the sandbox is really valuable for that.
[A: 09:27.5]
Makes sense. And the data import tool updates, are those also related to, like, testing and configuration?
[B: 09:34.5]
Those are more about making it easier to import large volumes of data into TME®, which is really important for companies that are growing quickly or need to integrate data from lots of different sources.
[A: 09:47.7]
So it's like streamlining that data onboarding process.
[B: 09:50.4]
Exactly.
[A: 09:51.0]
Okay, cool. And then I saw something about new inventory permissions.
[B: 09:55.0]
Yeah.
[A: 09:55.7]
What's that all about?
[B: 09:56.7]
Those are all about security.
[A: 09:58.0]
Oh, okay.
[B: 09:58.7]
So now administrators have really granular control over who can see what items in the inventory.
[A: 10:04.9]
So it's like an extra layer of protection.
[B: 10:06.7]
Exactly. Especially for companies that deal with sensitive or proprietary components.
[A: 10:11.3]
Right. You don't want just anyone to be able to access that information.
[B: 10:13.9]
No, absolutely not.
[A: 10:14.8]
It's like having a high security vault for your most valuable assets.
[B: 10:18.4]
That's a great way to put it.
[A: 10:19.9]
So it seems like MASS Group has really put a lot of thought into this update.
[B: 10:24.4]
Oh, yeah.
[A: 10:25.1]
They've not only added these big, flashy features.
[B: 10:28.1]
Right.
[A: 10:28.6]
But they've also paid attention to all those little details that really make a difference in terms of user experience.
[B: 10:35.1]
Absolutely. It's clear that they're committed to making TME as user friendly and flexible as possible.
[A: 10:41.8]
Okay, so we've talked about this update, all the new features, enhancements and tweaks, but let's step back for a second.
[B: 10:48.4]
Yeah.
[A: 10:49.0]
And talk about the why.
[B: 10:50.5]
All right.
[A: 10:51.1]
Why did MASS Group decide to focus on these specific areas?
[B: 10:55.6]
they talk about empowering semiconductor manufacturers to tackle defects with confidence and to optimize every stage of their processes. And this update really reflects that mission.
[A: 11:06.8]
So it's not just about adding bells and whistles to their software.
[B: 11:10.3]
No.
[A: 11:10.7]
It's about giving manufacturers the tools they need to really excel in this industry.
[B: 11:15.7]
Exactly. It's about helping them be more efficient, more reliable, and ultimately more profitable.
[A: 11:21.6]
Yeah.
[B: 11:22.1]
It's about having that clarity and guidance that allows manufacturers to stay ahead of the curve and navigate the complexities of semiconductor manufacturing. You know, imagine you're an engineer in a semiconductor fab. And instead of spending hours poring over spreadsheets or chasing down these elusive defects, now you can access real time data, you can visualize complex patterns, and you can get a really clear picture of what's happening at every stage of production.
[A: 11:49.7]
Yeah. It's like going from this, like, dimly lit room to a brightly illuminated space. You can finally see everything with clarity and precision.
[B: 11:58.7]
And with that clarity comes a sense of empowerment. So you're no longer just reacting to problems, you're anticipating them, you're preventing them, and you're really driving that continuous improvement.
[A: 12:09.0]
It sounds like a much more engaging and rewarding way to work.
[B: 12:11.8]
It is.
[A: 12:12.5]
Instead of feeling like just a cog in a giant machine, you're now the conductor.
[B: 12:17.5]
You know, it's an exciting time to be following the semiconductor industry. I'm really eager to see what the future holds.
[A: 12:22.4]
Me too. And to our listeners, thank you for joining us on this deep dive into the world of MASS Group and this groundbreaking new update. We'll see you next time for another fascinating exploration of the cutting edge of technology and its impact on our world.
Enhanced Defect Tracking
Traditional defect tracking methods can be rigid and limiting. MASS Group’s updates introduce customizable defect libraries, giving manufacturers the flexibility to define and manage defect categories that fit their unique workflows—think tailored solutions rather than one-size-fits-all.
Real-Time Data Visualization
Dynamic tools like heat maps and Pareto charts enable manufacturers to quickly identify patterns and trends. These visualizations turn raw data into actionable insights, empowering faster responses to defects.
Interactive Wafer Mapping
With the addition of wafer mapping, manufacturers can pinpoint the exact location of defects, providing the critical context needed for effective root cause analysis. This granular view streamlines the troubleshooting process and improves overall product quality.
Defect Collection API
Seamlessly integrate data from multiple systems into a centralized hub with the new defect collection API. This holistic approach ensures no detail is overlooked and accelerates decision-making.
Learn More in Our Release Notes Blog
Dive deeper into the latest TME® updates and discover how they’re reshaping semiconductor manufacturing.
Explore the full blog post here: Tackling Defects with Data: New Release Boosts Semiconductor Quality Control
Looking Ahead
As semiconductor manufacturing becomes increasingly complex, staying ahead of the curve requires the right tools. With these innovative updates, MASS Group continues to empower manufacturers to tackle challenges with confidence and precision.
Want to see these tools in action? Schedule a demo with MASS Group today.
Subscribe to The Root Cause Podcast on YouTube or follow MASS Group on LinkedIn for more insights into manufacturing, automation, and innovation. Stay tuned for more episodes that dive deep into the trends shaping the future of this exciting industry!