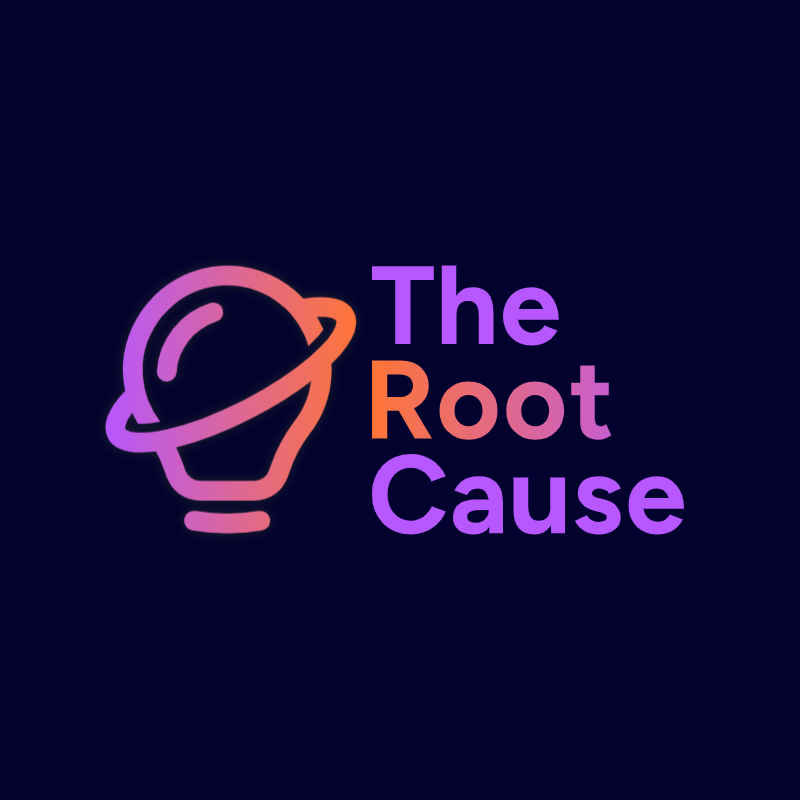
How Your ERP Is Limiting Your ROI in Manufacturing
The Root Cause Podcast Ep. 16 - ERP Isn't Enough in Modern Manufacturing: How Its Limitations Are Impacting Your ROI
In this episode of 𝘛𝘩𝘦 𝘙𝘰𝘰𝘵 𝘊𝘢𝘶𝘴𝘦, we uncover the real reason your ERP system might not be delivering the performance—and ROI—you expected. Below is What We Address in Episode 16:
-
Why ERP systems fall short on the shop floor
-
The telltale signs your ERP is underperforming
-
How MES, WMS, and CMMS bridge critical execution gaps
-
A 5-phase ERP optimization framework to drive real results
If you’ve already invested in ERP or are planning to, this episode is a must-listen.
[A: 00:07.9]
If you're listening to this, chances are you're in the manufacturing world.
[B: 00:12.1]
Yeah.
[A: 00:12.4]
And if you're in manufacturing, you've probably either taken the plunge already, made a big investment in an ERP system, or maybe you're thinking about it. You know, it's supposed to be the backbone of your whole operation.
[B: 00:24.3]
Right.
[A: 00:25.0]
The big question, though is, is ERP enough on its own? Can it really get you to that, you know, peak performance and the ROI that everyone's hoping for?
[B: 00:35.5]
It's a question that we hear a lot.
[A: 00:38.0]
Yeah.
[B: 00:38.6]
And it doesn't always get the attention it deserves.
[A: 00:41.5]
Right. We're going to dive deep into that today.
[B: 00:43.4]
Yeah. Because just having an ERP system up and running, you know, lights are blinking, that doesn't mean it's working the way it should or that you're getting that return on your investment.
[A: 00:52.9]
Exactly. So in this deep dive, we're going to unpack why even those. Those really powerful ERP systems, sometimes they just don't cut it on their own. We'll look at all those workarounds people are still doing manually. The data that's stuck in its own little computer compartments, the slow adoption, you know, people just not using the system like they should, and those blind spots that pop up on the shop floor, the things your ERP just doesn't seem to catch.
[B: 01:17.2]
Absolutely. And to really get a handle on this, we should be clear about what we mean by ERP ROI for a manufacturer.
[A: 01:24.0]
Yeah.
[B: 01:24.6]
Basically, it boils down to the value you're getting out of your ERP system. Things like, you know, better efficiency, lower costs, smarter decisions. You compare that to the total cost of the system, not just the initial price tag, but the implementation, the training, the upkeep, all of it.
[A: 01:42.0]
Right. The whole package. And that's where things can get a little tricky. That's where we see this, like ERP ROI illusion. You've got the system, it's processing data. But those big returns you were expecting, they're just not there.
[B: 01:55.2]
Yeah. You see, all the time you get.
[A: 01:56.6]
These unexpected costs popping up. You need customizations. Are you constantly calling support? And then there's the inefficiencies, the things the ERP was supposed to fix, but they just keep hanging around.
[B: 02:05.8]
Yep.
[A: 02:06.4]
And then there's the people. If they're not actually using the system, you're not getting your money's worth.
[B: 02:12.3]
Right. Adoption is key. And, you know, it's interesting. ERP systems, at their core, they're often not great at handling what's happening down on the shop floor.
[A: 02:21.5]
Right.
[B: 02:21.9]
They're good at that high level stuff, the planning, managing the money, forecasting. But when you need to know what's happening right now in the production line, that's where they fall short.
[A: 02:31.9]
Okay, so let's dig into that. What are some of the roadblocks that manufacturers hit that really stop their ERP from working the way it should?
[B: 02:40.9]
Well, a lot of it comes down to people, to be honest. You get resistance to change. People get used to doing things a certain way.
[A: 02:47.5]
It's comfortable.
[B: 02:48.4]
Exactly. So a new system comes in, even if it's better, people might be skeptical, they might not want to learn new things.
[A: 02:54.4]
And that leads to the next problem, right?
[B: 02:56.4]
Yeah. If people aren't on board, you don't get good communication between teams. Like, your sales team needs to be putting order details into the system accurately. The production team needs to report problems right away. If that's not happening, the whole flow of information breaks down.
[A: 03:11.0]
It's like a chain reaction.
[B: 03:12.3]
Exactly. And then there's data migration. Moving all that old data from your old systems into the new ERP.
[A: 03:19.3]
Oh, that can be a nightmare.
[B: 03:20.4]
It can be really complex. Mistakes happen and it can delay everything. If it's not done carefully, you're not going to see those benefits you were hoping for.
[A: 03:27.8]
Right, right. And then there's that question of customization. How much do you change the ERP to fit your old way of doing things versus changing your operations to fit the ERP, which might actually be better in the long run?
[B: 03:42.3]
It's a tough one. If you customize too much, your system gets super complex, it's expensive to maintain, upgrades are a headache. But if you're too rigid, you might miss out on what the system can really do for you. It's a balancing act for sure.
[A: 03:55.8]
And what happens after the initial excitement of going live with the new erp?
[B: 03:59.6]
That's another danger zone. The implementation phase is over. Everyone's tired. But you can't stop there. You need to keep optimizing, keep training, keep finding ways to use the system better. If that momentum drops off, you're leaving potential on the table.
[A: 04:13.4]
So for our listeners out there, how can they tell if their ERP system is, you know, not pulling its weight? Are there any warning signs?
[B: 04:21.7]
Oh, yeah, there are definitely some red flags.
[A: 04:24.1]
Like what?
[B: 04:24.6]
For example, if your teams are still using spreadsheets for things that the ERP is supposed to handle. That's a big one. Or if different departments are still working in their own little bubbles with their own data. Even though you have this central ERP system
[A: 04:38.2]
that's not good.
[B: 04:39.6]
Not good. It means something's wrong with the integration or maybe people just aren't using the system properly. If you see a lot of manual data entry, that's another sign. And if you can't get a real time view of your production or your inventory without running a bunch of reports, that's a problem.
[A: 04:55.8]
Makes sense.
[B: 04:56.5]
And if you're hearing people complain that the system is clunky or doesn't do what they need it to do, or if you find yourself constantly having to work around the ERP instead of with it, that's a pretty clear sign that it's not delivering. If you're seeing, you know, three or more of these things in your operation, it's definitely time to take a hard look at your ERP.
[A: 05:14.1]
Okay, so we've talked about the problems. Now let's talk about solutions. How can manufacturers bridge that gap between what the ERP promises and and what it actually delivers day to day? I think this is where the idea of an MES comes in, right?
[B: 05:27.2]
Absolutely. You can think of your ERP as like the command center for your business. It's great for the big picture. Planning, finances, sales projections. But when you need to know what's happening on the shop floor right now, the actual making of the product, that's where an MES shines.
[B: 05:44.0]
It works with your ERP to fill in those gaps.
[A: 05:47.2]
So ERP is the strategic brain and MES is more like the boots on the ground, getting things done manager.
[B: 05:53.7]
That's a great way to put it. ERP often kind of stops at the edge of the shop floor, you know.
[A: 05:57.6]
Right, right.
[B: 05:58.2]
It might tell you to make a thousand widgets by Friday, but it won't tell you how those widgets are being made, what quality checks are happening, or if there are any holdups.
[A: 06:06.6]
So if we're just relying on ERP, what are we missing in those shop floor operations? You're missing the details, like real time quality data. ERP might record the final inspection, but an MES can track quality every step of the way. It can spot trends and flag problems right when they happen.
[A: 06:23.7]
You also lose that instant visibility into production. What's the status of each machine? How's that work order progressing and tying maintenance into your production schedule? That becomes a lot harder with just ERP.
[B: 06:36.2]
It's like trying to run a factory using last year's financial report.
[A: 06:39.7]
Exactly. You get the general idea, but you're blind to the day to day stuff, the potential problems.
[B: 06:44.5]
Okay, so let's get specific. Let's compare A factory running just ERP versus one with ERP and mes. What are some examples?
[A: 06:52.3]
Sure. Let's start with inventory tracking.
[B: 06:54.1]
Good one.
[A: 06:54.5]
With just ERP, you're tracking purchase orders for raw materials and when finished goods ship out. And MES adds real time visibility. You know exactly where each batch of material is, what workstation it's at, when it got there.
[B: 07:07.0]
So you're not wasting time hunting things down. Less waste, fewer delays, tighter control over inventory. Some manufacturers see a 5 to 10% drop in material losses after adding an MES.
[A: 07:19.2]
Wow, that's significant. What about managing the production process itself?
[B: 07:22.8]
ERP gives you the overall production schedule, right? The MES takes that and digitize the workflows on the shop floor. It can send work orders to machines, track progress, and even adjust the schedule if something unexpected happens.
[A: 07:35.4]
Like a machine breakdown.
[B: 07:36.7]
Exactly. It keeps things moving smoothly. What about equipment maintenance?
[A: 07:41.0]
Okay, yeah. ERP can record when a machine was serviced, but what does MES bring to the table there?
[B: 07:46.9]
So ERP might say, you know, machine four broke down, got fixed on Wednesday. That's reactive. And MES helps you move to predictive maintenance.
[A: 07:54.5]
I like the sound of that.
[B: 07:55.6]
It constantly gathers data from your equipment. Temperature, vibrations, cycle times. It can spot patterns that suggest a problem before it actually happens. Then you can schedule maintenance proactively.
[A: 08:06.7]
It's going to save a lot of headaches.
[B: 08:08.3]
Huge difference. Less downtime, more production, happier customers. For example, if the MES sees vibrations increasing in a machine, it can trigger a work order in the CMMS. Get that maintenance scheduled before things break down. ERP wouldn't know until production stopped.
[A: 08:25.1]
That's a smart system. Now, what about quality control and tracing a product's history?
[B: 08:30.6]
Your ERP handles the overall documentation, the compliance stuff, and MES provides that deep dive, the product genealogy. It tracks every step for each finished product. What materials went into it, which machines it used, timestamps for each operation, all the quality checks.
[A: 08:47.0]
So if there's a problem, you can pinpoint exactly where it happened.
[B: 08:49.6]
Exactly. You know which batches are affected, and you can take action fast. ERP often doesn't have that level of detail.
[A: 08:55.6]
And what about data collection and reporting? That's got to be a big difference between ERP and an integrated MES.
[B: 09:01.2]
Big time. ERP gives you summaries, maybe daily or weekly reports on production. MES captures everything in real time directly from the shop floor. Cycle times for each machine, reasons for downtime, production rates per shift.
[A: 09:13.7]
It's a much clearer picture, isn't it?
[B: 09:15.5]
It is. You understand not just what's happening, but why you can find bottlenecks, see inefficiencies, and make decisions based on real data.
[A: 09:24.3]
Makes sense.
[B: 09:25.0]
Yeah.
[A: 09:25.4]
You also mentioned machine integration, things like SPC and SCADA. Where does a typical ERP fall short there?
[B: 09:32.1]
Yeah. So standard ERP systems, they're usually not very good at talking directly to the machines on the floor.
[A: 09:38.3]
Right.
[B: 09:38.5]
That's where MES excels. It connects to your machines, to PLCs, all those shop floor systems. It gathers performance data automatically. That allows for continuous monitoring, automated responses to events. And you can use tools like SPC for advanced quality tracking and scada, which interacts directly with your machinery.
[B: 09:57.3]
ERP just isn't built for that level of real time interaction.
[A: 10:00.8]
So it's pretty clear that just installing an ERP and hoping it'll solve all your problems is. Isn't realistic.
[B: 10:06.3]
Yeah. You need other systems to work with it and you need a plan to optimize everything. We talked about an optimization framework earlier and maybe we can go into that in more detail.
[A: 10:13.3]
Yeah, let's do that.
[B: 10:14.2]
Okay. So the key thing to remember is that optimizing your ERP isn't a one time thing. It's a process.
[A: 10:20.4]
It's a journey. It's continuous improvement. We break it down into five phases. The first is Assess and Align. You figure out how you're actually using your ERP system right now, and then you see if that aligns with your business goals.
[B: 10:32.8]
So what are you trying to achieve exactly?
[A: 10:35.8]
More efficiency, less waste, better customer service. Is your ERP actually helping you get there?
[B: 10:41.9]
Gotcha.
[A: 10:42.8]
Once you know where you stand, you move to Phase Two. Standardize and Streamline.
[B: 10:48.1]
What does that entail?
[A: 10:49.3]
Basically, you look at your manufacturing processes, find the parts that are inefficient or redundant. Then if it makes sense, you change those processes to match the way your ERP works. Sometimes you might even need to redesign workflows to really take advantage of what the ERP can do.
[B: 11:05.0]
So you're making the system and the processes work together smoothly.
[A: 11:08.7]
That's the goal. And then of course, you've got to get your people on board.
[B: 11:11.6]
Right? That's crucial.
[A: 11:13.2]
Phase Three: Train and Adopt. You need good training programs to make sure everyone knows how to use the ERP system and that they're actually using it every day
[B: 11:21.5]
not just letting it sit there. Right. Ongoing training, support resources, and really promoting the system from within.
[A: 11:27.9]
Okay, so you've got the system aligned with your goals. Your processes are optimized, your people are trained. What's next?
[B: 11:34.2]
Now you start connecting things. Phase Four is Integrate and Extend. This is where you really boost the value of your ERP by linking it.
[A: 11:42.1]
With other systems like MES, WMS, CMMS.
[B: 11:45.4]
Exactly. MES for shop floor execution, real time data. WMS for managing your warehouse and inventory. CMMS for keeping your equipment in top shape. By integrating these systems, you create a much more powerful digital ecosystem.
[A: 11:59.5]
And how do you know if all this is working?
[B: 12:01.3]
That's the final phase. Measure and Iterate. You set up key performance indicators or KPIs that directly measure the things you identified back in the assess and align phase. Then you track those KPIs to see the impact of your ERP and all the connected systems.
[A: 12:16.0]
You're constantly checking and adjusting, always improving.
[B: 12:18.9]
You find areas for improvement, analyze the results, and then go back to the earlier phases. Keep optimizing. It's like a continuous improvement loop similar to Lean or Six Sigma.
[A: 12:28.3]
Makes sense. So ERP is the foundation, but it really shines when it's part of this connected network of systems.
[B: 12:35.2]
Absolutely.
[A: 12:36.3]
Let's talk more about those connections, especially MES, WMS and CMMS. Why are they so important for manufacturing today?
[B: 12:43.6]
As we've been saying, MES gives you that real time control on the shop floor, which ERP often lacks.
[A: 12:49.4]
Right.
[B: 12:49.9]
Then you've got WMS, which is all about optimizing your inventory and fulfillment. It tracks goods in your warehouse, manages picking and packing, reduces shipping errors, and often connects with transportation systems to streamline logistics.
[A: 13:03.4]
So everything flows smoothly.
[B: 13:04.7]
Right. For example, if your ERP forecasts a spike in demand, the WMS makes sure the right materials are ready for production, preventing delays.
[A: 13:12.8]
And what about CMMS? It's focused on keeping your equipment running. Right.
[B: 13:16.6]
That's it. CMMS stands for Computerized Maintenance Management System. It's essential for managing your assets and all the maintenance tasks you can schedule preventative maintenance, track work orders, manage spare parts, all that good stuff to prevent.
[A: 13:28.5]
Breakdowns and keep things running.
[B: 13:30.2]
Exactly. And the integration with MES is really powerful here. If the MES detects something unusual, like those vibrations in a machine, it can automatically trigger a work order in the cmms.
[A: 13:42.3]
That's proactive maintenance right there.
[B: 13:43.9]
That's it. You're preventing problems before they happen, instead of waiting for something to break down and then notifying the ERP.
[A: 13:50.1]
So the real magic happens when all these systems can talk to each other, share data, and give you a complete view of your operation.
[B: 13:56.9]
Absolutely. That's the connected manufacturing ecosystem. Your ERP, MES, WMS, and CMMS working together, sharing data in real time. You get a complete picture of everything from buying raw materials to shipping the finished product.
[A: 14:10.9]
You mentioned an analogy earlier about the brain and nervous system.
[B: 14:14.0]
Yeah.
[A: 14:14.4]
Can you explain how MES, WMS and CMMS fit into that along with erp?
[B: 14:19.1]
Sure. Think of ERP as the brain of your manufacturing operation. It handles the big picture thinking, the planning, the finances, the strategy. MES is like the nervous system. It sends real time information from the shop floor back to the brain so you're always aware of what's happening.
[B: 14:35.4]
WMS is like the hands taking care of the physical movement and storage of materials. And CMMS is the feet, making sure your equipment is well maintained and ready to go.
[A: 14:45.2]
I like that. Just like a body needs all those parts to function, a modern factory needs all these systems working together.
[B: 14:51.0]
Exactly.
[A: 14:52.0]
So for executives who want to get the most out of their ERP, what are some concrete steps they can take?
[B: 14:57.6]
A few key things. First, define your KPIs, the metrics you'll use to measure success.
[A: 15:02.9]
Okay.
[B: 15:03.6]
Then audit your current ERP usage. Find any bottlenecks, underutilized features, or areas where people aren't using the system.
[A: 15:11.1]
Make sure you're getting your money's worth.
[B: 15:12.6]
Absolutely. And clean up your data. Bad data leads to bad decisions. Invest in ongoing training to keep your people up to speed. Create a plan for integrating your ERP with those other systems like MES, WMS and CMMS focus on data flow and automation.
[A: 15:30.4]
So it's a combination of strategy and technology.
[B: 15:32.8]
That's it. And build a culture of continuous improvement. Keep reviewing your performance, get feedback from users, and always look for ways to optimize.
[A: 15:41.1]
So you're never really done, are you?
[B: 15:42.6]
Nope. It's an ongoing process. And look for quick wins, things you can improve right away. But also think long term. What are the strategic changes that will make your operation more resilient and efficient in the future?
[A: 15:54.7]
Great advice. Now I know MASS Group has some solutions in this space. Without getting too salesy, can you tell us how you help manufacturers with ERP optimization and integration?
[B: 16:05.7]
Sure. At MASS Group, we focus on helping manufacturers get more out of their existing ERP systems. We provide real time data capture and visibility, a flexible system architecture that integrates with other platforms, and a no code or low code approach for faster deployment.
[B: 16:21.7]
We're not about replacing your erp, we're about making it better, especially in areas like shop floor execution, data insights, and integration.
[A: 16:30.1]
So the key takeaway is that ERP is important, but it's not the whole story.
[B: 16:34.5]
Right.
[A: 16:35.0]
To really excel, you need to optimize it and connect it with other systems. It's not a one size fits all solution.
[B: 16:40.3]
Exactly. Think of ERP as the foundation for building a smarter, more connected, more successful manufacturing operation.
[A: 16:47.6]
That's a great way to put it. So to our listeners, I want you to think about the hidden potential in your own ERP system. By focusing on optimization and connecting your planning and execution processes, you can gain a real competitive advantage.
[B: 17:02.1]
Absolutely.
[A: 17:02.8]
Thanks for joining us for this deep dive. We'll see you next time.
Subscribe to The Root Cause Podcast on YouTube or follow MASS Group on LinkedIn for more insights into manufacturing, automation, and innovation. Stay tuned for more episodes that dive deep into The Root Cause!