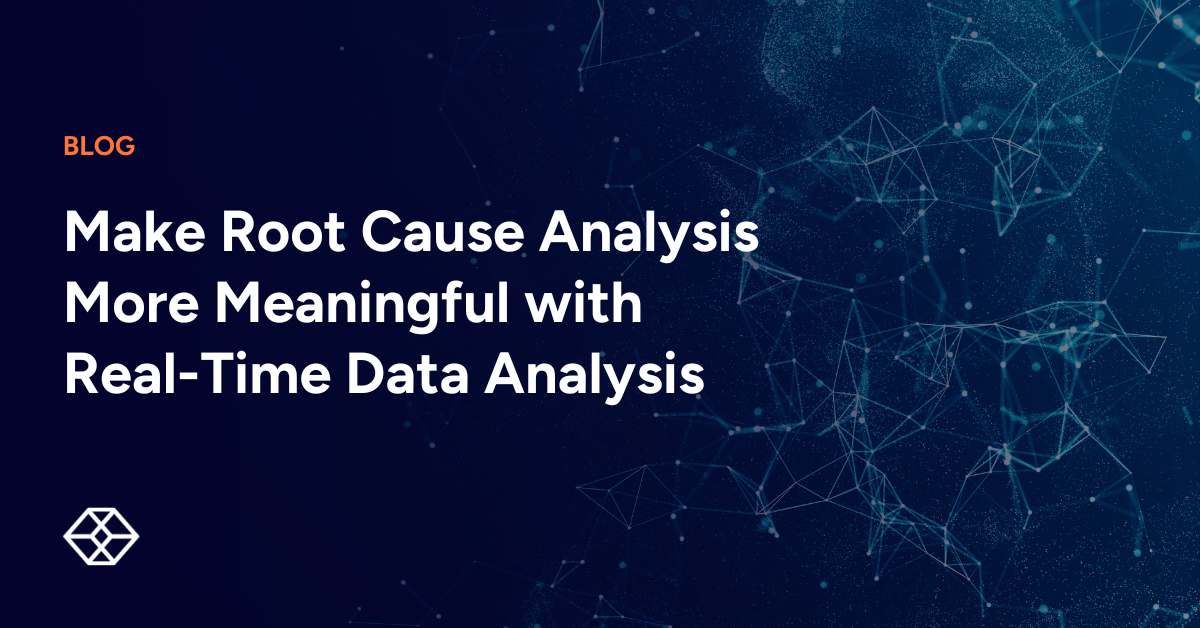
How Advanced Analytics Is Transforming Root Cause Analysis
When the stakes are high, things can—and often do—go awry. It's classic Murphy’s Law.
To move beyond a pattern of problems, manufacturers must understand the problems’ underlying source. Enter root cause analysis (RCA).
This is a cornerstone practice in manufacturing.
The systematic analysis has, for years, helped manufacturers identify the source of problems and find effective solutions. But, advancements in data analysis and technology are transforming the RCA process. Today’s version is faster, more precise, and indispensable in a competitive landscape.
A Brief History of RCA
Root cause analysis provides a repeatable structure for problem-solving within manufacturing. It’s also a crucial component of lean manufacturing and Six Sigma.
Getting to the root of a problem quickly starts by asking “why.”
This simple problem-solving technique appears throughout history. Plato’s Meno illustrates how a structured, inquisitive approach can lead to a deeper understanding of underlying issues. Or, for a more modern RCA example, consider the “Five Whys” technique developed by The Toyota Motor Corp. This circa-1950s approach had a major influence on RCA's modern form.
In general, RCA can be simplified into four steps:
- Identify and clearly describe the problem.
- Establish a timeline from the normal situation until the problem occurred.
- Distinguish between the root cause and other symptomatic or causal factors.
- Establish a causal graph between the root cause and the problem.
The point is to identify and address the root of each issue to prevent similar problems from occurring again.
For instance, a manufacturing RCA might point to human error caused by fatigue or miscommunication, process failures caused by ad-hoc workflows, or equipment failures caused by defects or delayed maintenance. Once discovered, the cause of the issue can be effectively fixed.
Data’s Role in 21st-Century RCA
With today’s advancements, data and systematic questioning work hand-in-hand to make RCA more powerful. Asking iterative “why” questions reveals patterns, while data provides the evidence to validate the resulting insights.
In factories where processes vary in optimization, RCA becomes invaluable. It helps organizations address root causes and implement long-term solutions that improve reliability, safety, and efficiency. These improvements are reflected in reduced downtime, fewer defects, and higher quality, safety, and efficiency.
The challenge? Data management.
In order to effectively perform the steps of an RCA, organizations need to identify dates, times, and locations of problems. Teams need to track down detailed documentation, reports, and other information. Unfortunately, a lot of companies find that essential information is often missing or incomplete.
Automation could be helpful here. The concept of monitoring everything and storing all that data long term is appealing. But that creates a new challenge of its own. Industry 4.0, with its use of smart sensors and interconnected technologies, creates a huge volume of data. Too much for anyone to manually sort through. It can make RCA feel like finding a needle in a haystack. For a more in-depth analysis of the history and future of root cause analysis, visit the link here for MASS Group's latest podcast episode!
How Tech Enhances Root Cause Analysis
There is good news for this data-rich reality: Machine learning and artificial intelligence are reshaping how manufacturers identify and correct problems. With these capabilities on board, teams can quickly detect patterns and relationships in complex data, making RCA faster and more accurate.
One of the best ways to access this processing power? Through a manufacturing execution system (MES).
At MASS Group, we implement MES's that are designed to give manufacturers a full view of their operations. Our MES supports root cause analysis through real-time data collection, analysis, and reporting capabilities. This enables factories to identify and address issues with more precision and speed.
With this platform, manufacturers can seamlessly gather and analyze data across multiple sources, collaborate with stakeholders, and track the effectiveness of corrective actions, all in a single, unified platform.
Want to see how TME® can optimize your operations? Schedule a demo.